FEP masterbatch is a granular product made from polytetrafluoroethylene (FEP) resin as a carrier, with the addition of pigments, dispersants, and other additives. It belongs to a type of fluorine masterbatch. Its chemical structure endows the material with unique properties, such as excellent chemical resistance, temperature resistance, and electrical performance. FEP masterbatch is prepared by liquid-phase method or melt extrusion process to ensure uniform dispersion of pigments in the resin. By combining FEP resin with specific additives, color customization and functional modification are achieved, and it is widely used in high-end manufacturing fields.
Characteristic
Chemical resistance
Almost insoluble in any organic solvent, resistant to strong acids, alkalis, and corrosive chemicals, suitable for harsh environments such as chemical and semiconductor industries.
Temperature resistance
The long-term temperature range is -200 ℃ to 200 ℃, and the short-term temperature resistance can reach 260 ℃, meeting the requirements of extreme temperature scenarios.
Electrical performance
It has excellent insulation performance and low dielectric constant (≤ 2.15), suitable for high-frequency and high-speed data transmission, such as in the field of 5G communication.
Mechanical properties
High strength, high toughness, strong impact resistance, elongation at break ≥ 280%, suitable for manufacturing structural components under complex working conditions.
Transparency and Optical Performance
High transmittance and low haze, suitable for optical films, architectural films, and other fields such as solar panel packaging.
Processability
Excellent fluidity, capable of forming complex shapes through processes such as blow molding, extrusion, injection molding, etc., with minimal performance loss during processing.
Environmental Protection and Safety
Compliant with ROHS standards, free of heavy metals such as cadmium, lead, chromium, etc., it can be used for food contact grade applications (such as medical device components).
Types
FEP masterbatch can have multiple types according to different classification standards. The following are some common classification methods and corresponding types:
مصنفة حسب الغرض
Injection grade FEP masterbatch: With good fluidity and formability, it is suitable for injection molding processes and can be used to manufacture various complex shaped plastic products, such as electronic component casings, chemical pipeline connectors, etc.
Extrusion grade FEP masterbatch: with moderate fluidity and good tensile properties, mainly used in extrusion processes, such as the production of wire and cable insulation layers, pipes, films, etc.
Coating grade FEP masterbatch: With excellent film-forming and adhesion properties, it is commonly used to coat surfaces of other materials to provide properties such as corrosion resistance, high temperature resistance, and low friction coefficient, such as coating metal sheets, glass fibers, etc.
According to the classification of additives
Enhanced FEP masterbatch: By adding reinforcing materials such as glass fiber and carbon fiber, the mechanical strength, hardness, and wear resistance of FEP masterbatch can be improved. It is suitable for applications that require high mechanical properties, such as component manufacturing in aerospace, automotive manufacturing, and other fields.
Conductive FEP masterbatch: Added with conductive fillers such as carbon black, metal powder, etc., to give it a certain degree of conductivity, it can be used to manufacture anti-static or electromagnetic shielding products, such as electronic device casings, wire and cable shielding layers, etc.
Flame retardant FEP masterbatch: Added with flame retardant, it has good flame retardant properties, can effectively prevent product combustion, improve usage safety, and is commonly used in places with high fire protection requirements, such as related products in the construction, power and other industries.
Classification based on fluorine content
High fluorine content FEP masterbatch: With a high fluorine content, generally above 60%, it has superior chemical stability, high temperature resistance, and low friction coefficient. It is suitable for some special fields with extremely demanding performance requirements, such as high-end chemical engineering, aerospace, etc.
FEP masterbatch with moderate fluorine content: With a fluorine content between 50% and 60%, it has good comprehensive performance and relatively moderate price. It is a common type in the market and widely used in general industrial fields such as electronics, electrical, and chemical engineering.
Low fluorine content FEP masterbatch: With a fluorine content between 40% and 50%, the cost is relatively low, but its performance may be reduced compared to FEP masterbatch with high and medium fluorine content. It can be used in some fields that are not particularly strict in performance requirements but are sensitive to cost, such as civil plastic products.
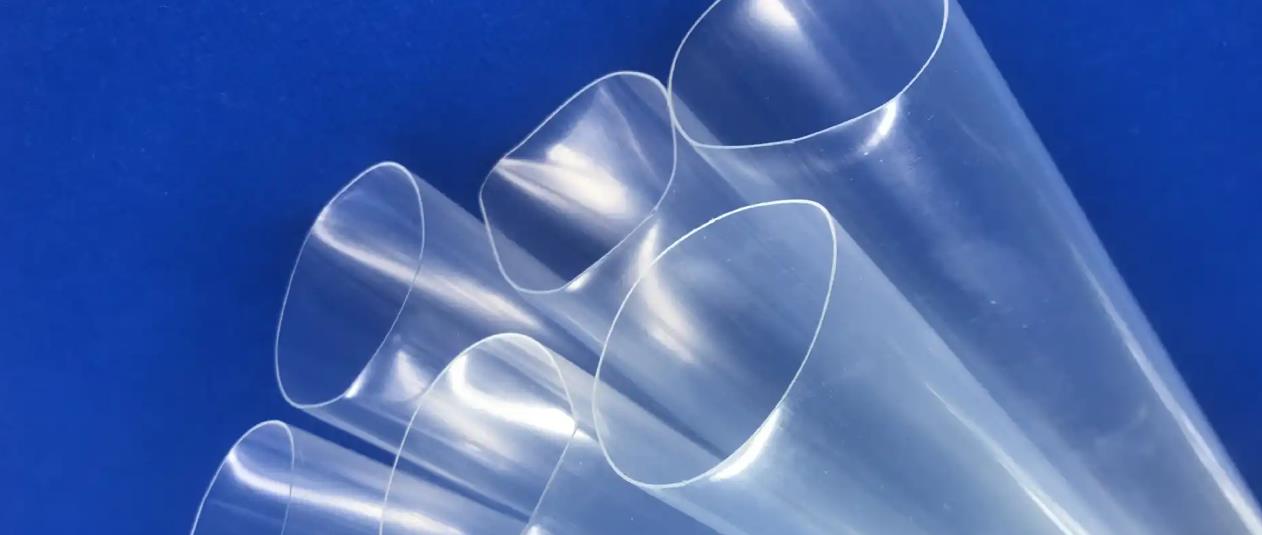
نسبة الصيغة
FEP color masterbatch
Pigments or dyes: 5% -15%. For example, in the preparation of deep blue FEP masterbatch, the amount of reactive dye can account for 5% -15%, which can be adjusted according to the required color depth.
Carrier resin (FEP resin): 70% -90%. Provide basic performance and molding characteristics for color masterbatch, ensuring compatibility between color masterbatch and target plastic.
Dispersant: 0.5% -5%. Assist in the uniform dispersion of pigments or dyes in the carrier resin, improving the coloring effect and stability of color masterbatch.
Additives (such as brighteners, stabilizers, etc.): 0.1% -2%. Add as needed to improve the performance of color masterbatch, such as increasing glossiness, enhancing stability, etc.
Enhanced FEP masterbatch
FEP resin: 60% -80%. As the matrix material of the masterbatch, it provides basic properties such as chemical corrosion resistance and high temperature resistance.
Reinforcement materials (such as glass fiber, carbon fiber, etc.): 10% -30%. By selecting the appropriate dosage based on the requirements for the mechanical strength, hardness, and wear resistance of the masterbatch, the mechanical properties of the masterbatch can be significantly improved.
Dispersant: 0.5% -3%. Helps to evenly disperse the reinforcement material in FEP resin and improve the reinforcement effect.
Coupling agent: 0.1% -2%. Used to improve the interfacial bonding strength between reinforcement materials and FEP resin, and enhance the comprehensive performance of masterbatch.
Other additives (such as antioxidants, light stabilizers, etc.): 0.1% -2%. Add according to the usage environment and requirements to improve the stability and weather resistance of the masterbatch.
Flame retardant FEP masterbatch
FEP resin: 65% -85%. Ensure the basic properties of the masterbatch, such as processing performance, chemical corrosion resistance, etc.
Flame retardant: 10% -25%. Choosing the appropriate flame retardant and its dosage according to the required flame retardant level can effectively prevent the combustion of the masterbatch.
Synergistic agent: 0.1% -5%. Used in conjunction with flame retardants to improve flame retardancy, reduce the amount of flame retardants used, and minimize their impact on other properties of the masterbatch.
Antioxidant: 0.1% -2%. Prevent FEP resin from degrading due to oxidation during processing and use, and improve the stability of masterbatch.
Lubricant: 0.5% -2%. Improve the processing flowability of masterbatch to make extrusion or injection molding processes smoother.
Conductive FEP masterbatch
FEP resin: 60% -80%. As the main body of the masterbatch, it provides basic properties such as insulation and chemical corrosion resistance.
Conductive fillers (such as carbon black, metal powder, etc.): 10% -30%. Adjust the addition amount according to the requirements for the conductivity of the masterbatch, so that the masterbatch has a certain conductivity and can be used for anti-static or electromagnetic shielding purposes.
Dispersant: 0.5% -5%. Assist in the uniform dispersion of conductive fillers in FEP resin, improving the stability and consistency of conductivity performance.
Coupling agent: 0.1% -2%. Improve the bonding strength between conductive fillers and FEP resin, and enhance the mechanical and electrical properties of the masterbatch.
Other additives (such as antioxidants, light stabilizers, etc.): 0.1% -2%. Add according to the usage environment and requirements to improve the stability and weather resistance of the masterbatch.
The above formula ratios are for reference only. In actual production, adjustments and optimizations need to be made based on specific application requirements, raw material characteristics, production equipment, and processes.
عملية الإنتاج
The production process of FEP masterbatch generally includes the following main steps:
Raw material preparation
FEP resin: Select the appropriate type of FEP resin based on product performance requirements, check its purity, molecular weight distribution, and other indicators to ensure compliance with production standards.
Additives: Accurately weigh various additives, such as antioxidants, light stabilizers, lubricants, pigments, etc., to ensure the quality and accurate amount of additives.
Mix
Add FEP resin and additives to the high-speed mixer for thorough mixing. During the mixing process, it is important to control the mixing speed and time. Generally, the mixing speed is between 500-1000 revolutions per minute and the mixing time is between 10-30 minutes to ensure that the additives are evenly dispersed in the FEP resin. For some difficult to disperse additives, pre dispersion treatment can be carried out first.
Squeeze out
Melt extrusion: Add the mixed material into a twin-screw extruder for melt extrusion. The temperature setting of the extruder is crucial. Generally, the temperature gradually increases from the feeding section to the head, with the feeding section temperature controlled at 200-220 ℃, the compression section temperature at 250-280 ℃, the metering section temperature at 280-300 ℃, and the head temperature at 300-320 ℃. According to the characteristics of different FEP resins and additives, the temperature may need to be adjusted appropriately.
Screw speed: The screw speed is usually between 100-300 revolutions per minute. If the speed is too fast, it may cause uneven material mixing or overheating degradation, while if the speed is too slow, it will affect production efficiency. By adjusting the screw speed and temperature, the material is fully melted, mixed, and plasticized in the extruder.
Granulation
Underwater pelletizing: The extruded material is extruded into strips through a die and then enters the underwater pelletizer. In the underwater granulator, the high-speed rotating cutter cuts the strip material into particles, with a cutting speed generally between 500-1500 revolutions per minute. The cutter speed and feeding speed are adjusted according to the particle size requirements.
Air cooling or water cooling: The cut particles are cooled by an air cooling or water cooling system to quickly cool and shape the particles, preventing particle adhesion or deformation. The air-cooled system blows cold air towards the particles through a fan, while the water-cooled system cools the particles through a water tank. The moisture content of the cooled particles should be controlled below 0.1%.
Screening and packaging
Screening: The cooled FEP masterbatch is sieved through a vibrating screen to remove oversized or undersized particles and potential impurities. The commonly used mesh size is between 20-80 mesh, and the appropriate mesh size should be selected according to the product specifications.
Packaging: Qualified FEP masterbatch after screening is packed into sealed bags or packaging bags. During the packaging process, attention should be paid to preventing the masterbatch from getting damp or contaminated. For products that require high moisture resistance, desiccants can be added to the packaging bags. Packaged masterbatch should be stored in a dry and ventilated warehouse, avoiding direct sunlight and high temperature environments.
Throughout the entire production process, it is necessary to conduct quality inspections on each batch of products, including testing of appearance, particle size distribution, melt flow rate, thermal stability, mechanical properties, and other indicators, to ensure that product quality meets standard requirements. At the same time, production process parameters should be adjusted in a timely manner based on the actual situation during the production process, such as equipment operation status, product quality feedback, etc., to ensure the stability of production and consistency of product quality.
معدات الإنتاج
The equipment for producing FEP masterbatch mainly includes the following types:
معدات الخلط
High speed mixer: used to thoroughly mix FEP resin with various additives. It usually consists of a mixing container, stirring blades, driving motor, etc. The stirring blade rotates at high speed under the drive of the motor, causing strong convection and shear effects on the material inside the container, thereby achieving uniform mixing. It has the advantages of fast mixing speed and good mixing effect.
معدات البثق
Twin screw extruder: It is one of the key equipment for FEP masterbatch production. It mainly consists of two parallel screws, a material cylinder, a heating and cooling system, a transmission device, etc. Two screws rotate synchronously in the material barrel. After the material enters the barrel from the hopper, it moves forward under the push of the screws, and gradually melts and plasticizes under the shearing, squeezing, and heating effects of the screws. Twin screw extruders have good mixing, dispersing, and conveying capabilities, which can ensure the uniformity and stability of materials during the extrusion process.
معدات التحبيب
Underwater granulator: mainly composed of cutting blade, template, water chamber, transmission device and other parts. The molten material extruded by the extruder is extruded into strips through the small holes on the template, and after entering the water chamber, it is cut into particles by the high-speed rotating cutter. The underwater pelletizer has the advantages of fast pelletizing speed, regular particle shape, and smooth surface, and can produce high-quality FEP masterbatch.
Air cooling or water cooling system: used for cooling and shaping the cut FEP masterbatch. Air cooling systems generally consist of fans, air ducts, etc., which blow cold air towards particles through the fans to rapidly cool them down. The water cooling system includes equipment such as a water tank and a water pump. When particles pass through the water tank, they exchange heat with the water to achieve cooling.
Screening equipment
Vibration screen: usually composed of screen box, vibration motor, spring and other components. The vibration motor drives the sieve box to perform high-frequency vibration, causing the FEP masterbatch to bounce on the sieve, thereby achieving the separation of particles of different sizes. By replacing screens with different mesh sizes, it is possible to screen out mother particles that meet the particle size requirements, remove particles that are too large or too small, and remove impurities.
معدات التعبئة والتغليف
Automatic packaging machine: capable of automatically completing packaging processes such as measurement, filling, and sealing. It mainly consists of measuring device, filling device, sealing device, control system, etc. By setting the packaging weight or quantity, the automatic packaging machine can accurately pack FEP masterbatch into the packaging bag and complete the sealing operation, improving packaging efficiency and quality. At the same time, some packaging machines also have functions such as labeling and coding, which facilitate product identification and traceability.
In addition to the main equipment mentioned above, the production of FEP masterbatch may also require some auxiliary equipment, such as raw material drying equipment, feeding equipment, storage tanks, etc., to ensure the smooth progress of the production process.
FEP masterbatch extruder
Kerke’s masterbatch extruder can be used to produce FEP masterbatch. Our FEP masterbatch extruder has multiple models to choose from, which can meet different production requirements.
-
آلة البثق اللولبية المزدوجة للمختبر
متى ستحتاج إلى آلة بثق ثنائية اللولب للمختبر؟ إذا كنت ترغب في إجراء تجارب واختبارات...
-
آلة البثق ذات اللولب المزدوج المتوازي
تم تصميم آلة البثق ذات المسمار المزدوج ذات الدوران المتوازي لدينا لتصنيع المركبات والدفعات الرئيسية مع سعة إنتاج تتراوح من...
-
طارد ثلاثي (3 براغي)
آلة البثق ثلاثية البراغي هي تقنية جديدة ذات مزايا عديدة. تُستخدم آلة البثق ثلاثية البراغي بشكل رئيسي...
-
نظام البثق ثنائي المرحلة
تم تصميم نظام بثق الأم والطفل للمواد الخاصة التي لا يمكن معالجتها على مرحلة واحدة من البثق، المرحلة الأولى...
-
خط تصنيع العجنات في بانبوري
تم تصميم آلة العجن والبثق الخاصة بنا لصنع تطبيقات خاصة بسعة إنتاج تتراوح من 30 كجم / ساعة إلى 1000 كجم / ساعة.
-
نظام القطع / نظام التكوير
تحتاج المواد المختلفة إلى نظام قطع مختلف، توفر شركة Kerke جميع أنواع أنظمة القطع، فيما يلي شرح لها…
Related requirements
The extruder is a key equipment for producing FEP masterbatch, and it has the following requirements:
Screw design
High shear mixing ability: In the production of FEP masterbatch, screws are required to provide strong shear force to ensure thorough and uniform mixing of FEP resin and additives. The design of the screw edge shape, pitch, and thread depth needs to be optimized to enhance shear and mixing effects, promote uniform dispersion of additives in the resin, and avoid local uneven mixing.
Strong adaptability: able to adapt to the characteristics of FEP resin and various additives. Due to the possible differences in melting characteristics, viscosity, and other aspects between different batches of FEP resin and additives, screw design should have a certain degree of flexibility. By adjusting parameters such as screw combination or speed, stable extrusion processes can be achieved under different raw material conditions.
Temperature control
Accurate temperature control: FEP masterbatch production requires strict temperature control, and the temperature of each section of the extruder needs to be precisely controlled. Generally, the temperature gradually increases from the feeding section to the machine head. The temperature in the feeding section is usually controlled at 200-220 ℃, the compression section at 250-280 ℃, the metering section at 280-300 ℃, and the machine head at 300-320 ℃. Minor temperature fluctuations can affect the quality of FEP masterbatch, such as excessive temperature leading to FEP resin degradation and affecting product performance; If the temperature is too low, it will cause poor plasticization of the material, resulting in uneven particle surfaces and internal structures. Therefore, the extruder needs to be equipped with a high-precision temperature control system, such as thermocouples, temperature controllers, etc., to achieve precise measurement and adjustment of the temperature in each section.
Quick response: During the production process, when parameters such as raw material formula and extrusion speed change, the temperature control system should be able to quickly respond and adjust to a new stable temperature state. For example, when different melting point additives are replaced or the extrusion speed is adjusted, the temperature of each section of the extruder can be stabilized at the set value in a short period of time to ensure the continuity of production and the stability of product quality.
Pressure stability
Pressure uniformity: During the extrusion process, the pressure exerted by the screw on the material should be uniform and stable. Only with uniform pressure can the flow velocity of materials in the extruder be ensured to be consistent, avoiding local accumulation of materials or excessive flow velocity. This is crucial for ensuring the particle size uniformity and product quality stability of FEP masterbatch. If the pressure fluctuates greatly, it can cause uneven thickness of the extruded masterbatch, and even defects such as bubbles and voids.
Pressure regulation range: The extruder should have a wide pressure regulation range to adapt to different production process requirements and raw material characteristics. For example, in the production of FEP masterbatch with different specifications or formulas, by adjusting parameters such as screw speed and back pressure, the extruder can work stably under different pressure conditions to ensure product quality meets requirements.
Production and efficiency
High output: To meet market demand, extruders should have a high production capacity. By optimizing parameters such as screw diameter, aspect ratio, and rotational speed, the conveying and extrusion efficiency of materials can be improved, achieving high yield per unit time. For example, using a large-diameter screw and a suitable aspect ratio design can not only increase the filling amount of materials, but also ensure that the materials have sufficient residence time in the extruder for sufficient plasticization and mixing, thereby increasing production while ensuring product quality.
Energy saving and efficient: While pursuing high output, attention should be paid to the energy-saving performance of the extruder. Adopting efficient motors, reducers, and heating and cooling systems to reduce equipment energy consumption. For example, by using energy-saving motors and intelligent temperature control systems, the heating power and cooling water volume can be automatically adjusted according to actual production needs, avoiding energy waste and reducing production costs.
Equipment material and corrosion resistance
Wear resistance: FEP resin and additives will cause certain wear on the screw and barrel during the extrusion process, especially for formulas containing fillers or reinforcing agents, where wear is more pronounced. Therefore, the screw and barrel of the extruder need to be made of materials with good wear resistance, such as nitride steel, bimetallic alloy steel, etc., to extend the service life of the equipment, reduce maintenance costs and downtime.
Corrosion resistance: Some corrosive additives, such as certain pigments or additives, may be used in the production of FEP masterbatch. In addition, FEP resin may also decompose and produce corrosive gases at high temperatures. Therefore, the internal contact parts of the extruder should have good corrosion resistance to prevent equipment from being corroded and damaged, which will affect product quality and production efficiency. The corrosion resistance of the screw and barrel can be improved by surface treatment, such as hard chromium plating, spraying corrosion-resistant coatings, etc.
طلب
FEP masterbatch has excellent properties such as chemical corrosion resistance, high temperature resistance, and electrical insulation, making it widely used in various fields. The following are some of the main application areas:
الأسلاك والكابلات
Insulation layer: FEP masterbatch can be used to produce insulation layers for wires and cables, which can maintain good insulation performance in high temperature environments and ensure the safety and stability of power transmission. For example, in fields such as aerospace and electronic equipment that require high performance of wires and cables, FEP insulated wires and cables are widely used.
Sheath: The sheath made of FEP masterbatch has characteristics such as wear resistance and chemical corrosion resistance, which can effectively protect the conductors and insulation layers inside the wire and cable, and extend the service life of the cable. In some harsh industrial environments, such as chemical companies, mines, etc., using FEP sheathed wires and cables can better resist external erosion.
Electronic appliances
Electronic component packaging: FEP masterbatch can be used for packaging electronic components, providing good protection to prevent the components from being affected by the external environment, while also having good electrical insulation performance to ensure the normal operation of the components. For example, some precision electronic chips, sensors, etc. often use FEP packaging materials.
Insulation film: The produced insulation film has excellent dielectric properties and high temperature resistance, and can be used for insulation isolation in electronic and electrical equipment, such as transformers, capacitors, and other equipment. It can effectively improve the performance and reliability of the equipment.
Automotive industry
Automotive wiring harness: FEP masterbatch is used for insulation and protection of automotive wiring harnesses, which can withstand high temperature environments such as engine compartments. It also has good oil and chemical resistance, ensuring the stable operation of automotive electrical systems.
Automotive parts coating: FEP coating can be applied to the surface of some automotive parts, such as engine components, fuel system components, etc., to achieve wear resistance, corrosion resistance, and high temperature resistance, improving the performance and service life of the parts.
المجال الطبي
Medical catheters: FEP masterbatch has good biocompatibility and chemical stability, and can be used to manufacture medical catheters such as central venous catheters, urinary catheters, etc. It can be used in the human body for a long time without adverse reactions, and its smooth surface helps reduce the risk of thrombosis.
Medical packaging: Packaging bags, boxes, and other medical packaging products made of FEP material have good barrier properties and radiation resistance, which can effectively protect the quality of medical supplies during storage and transportation, and can be disinfected through radiation sterilization and other methods.
مناطق أخرى
Food packaging: FEP masterbatch can be used to produce food packaging materials, such as food packaging bags, cling film, etc. It has good low temperature resistance and chemical stability, which can effectively maintain the freshness and quality of food, while complying with food hygiene and safety standards.
Building materials: In the field of construction, FEP masterbatch can be used to produce building materials with special properties, such as weather resistant and self-cleaning exterior wall coatings, roof waterproofing materials, etc. Its excellent UV resistance and chemical stability enable building materials to maintain good performance during long-term outdoor use.