EVA masterbatch is a granular material made mainly from ethylene vinyl acetate copolymer (EVA) and added with antibacterial agents, stabilizers, and other substances. EVA masterbatch has the characteristic of high safety, complying with the EU REACH regulation and RoHS directive requirements. Some products meet food grade requirements and do not precipitate or migrate. Widely used in various fields such as plastic products, building and decorative materials, printing inks, etc. For example, it has applications in children’s toys, medical and health materials, shoe materials, waterproofing membranes, sound insulation materials, decorative panels, and other fields.
Types
EVA masterbatch can be classified into the following types based on their functions and purposes:
1. EVA masterbatch: composed of EVA copolymer and pigment. EVA provides excellent softness, toughness, and weather resistance, which helps with the dispersion and stability of pigments. Pigments endow plastics with various desired colors, possessing excellent color expression, dispersion, and stability, and are widely used in the field of color enhancement for plastic products.
2. EVA foam masterbatch: generally composed of composite foaming agent, lubricant, dispersant, coloring agent, etc. Commonly used in the foam production of materials such as PE, PP, EVA, etc., it can make the products have good elasticity, softness, and cushioning performance, and is widely used in shoe materials, packaging materials, automotive interiors, and other fields.
3. EVA flame retardant masterbatch: It is a masterbatch composed of flame retardants, resins, and additives used for flame retardant modification of EVA materials. EVA products can have good flame retardant properties and meet the fire safety requirements of different application scenarios, such as wires and cables, electronic and electrical enclosures, etc.
4. EVA cooling masterbatch: also known as flow agent, heat stabilizer, etc. Adding it to the processing of EVA products can increase resin fluidity, improve melt index, reduce molecular weight accumulation, and thus lower processing temperature. It has the advantages of no pollution, no odor, and good dispersibility, and can be widely used in the processing of various plastics and related products.
5. EVA functional masterbatch: This is a relatively broad category, including but not limited to brightening masterbatch, antibacterial masterbatch, UV resistant masterbatch, weather resistant masterbatch, etc. Brightening masterbatch is used to improve the brightness of products; Antibacterial masterbatch can endow EVA products with antibacterial properties; UV resistant masterbatch and weather resistant masterbatch can improve the aging resistance and UV resistance of EVA products in outdoor environments, extending their service life.
6. EVA filling masterbatch: mainly composed of fillers (such as calcium carbonate, talc powder, etc.), coupling agents, dispersants, and carrier resin EVA. Adding it to EVA products can reduce costs and improve certain properties of the product, such as hardness and rigidity, to a certain extent.
7. EVA Silicone Masterbatch: It is an EVA dispersion of high concentration ultra-high molecular weight siloxane, which can effectively improve the flowability and demolding of plastic processing, reduce torque, reduce equipment wear, lower friction coefficient, improve the surface gloss and silky touch of products, and also has certain flame retardancy, which can improve the impact strength of flame retardant materials.
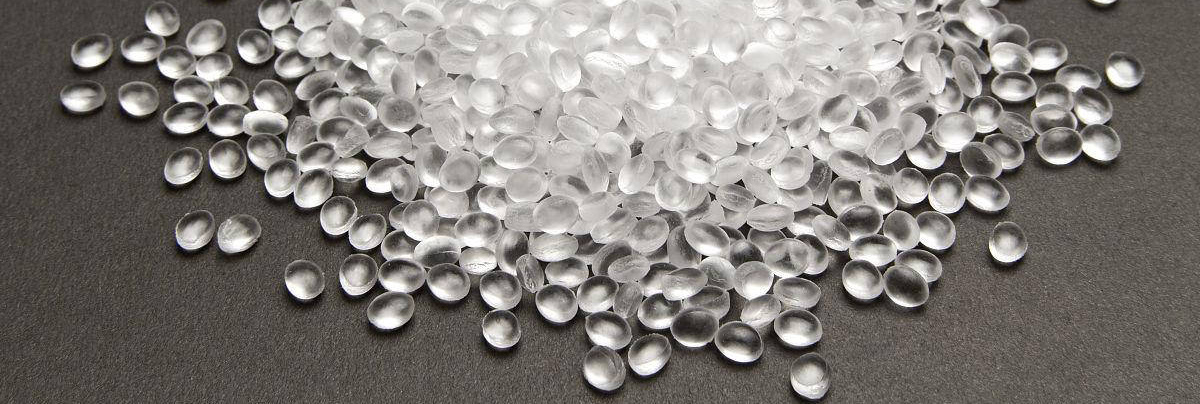
نسبة الصيغة
The following are common formula ratios for different types of EVA masterbatch:
EVA masterbatch:
Pigments: 15% -70%, if it is an inorganic pigment, the addition amount is usually between 50% -70%; Organic pigments account for 15% -50%.
EVA carrier resin: 10% -40%, generally using EVA resin with a VA content of about 18%.
Additives: 2% -4% zinc stearate, 4% -15% EVA wax, 0.5% -1% titanate coupling agent, and may also contain a small amount of antioxidants, UV absorbers, etc.
EVA foam masterbatch:
EVA resin: 35% -45%, can be a combination of different types of EVA, such as EVA634 and EVA MV1055 mixed in a mass ratio of 1:1.9-2.1.
Waste EVA: 20% -25%, can effectively reduce costs and improve certain performance.
elastomer: SEBS 10%-15%, Increase the elasticity and flexibility of the product.
Filler: 10% -15% talc powder, which can improve the hardness and dimensional stability of the product.
Foaming agent: AC 3%-5%, It is a key component in generating bubbles.
Crosslinking agent: DCP (diisopropylbenzene peroxide) 1.5% -3%, which causes cross-linking reaction of EVA molecules and improves product performance.
Other additives: Flow additives 2% -3%, amine modified zinc oxide 3% -5%, stearic acid 0.5% -0.8%, and may also include small amounts of zinc stearate, calcium stearate, etc.
EVA flame retardant masterbatch:
EVA resin: 88% -92%, the specific proportion is adjusted according to the resin melt index and product requirements.
Flame retardants: 8% -12%, such as FR-H617, have high thermal stability and photostability, which can endow EVA with good flame retardant properties.
EVA filled masterbatch:
EVA resin: usually accounting for 20% -40%, used as a carrier to evenly disperse fillers in EVA products.
Fillers: Calcium carbonate, talc powder, etc., accounting for 60% -80%, are the main components of filling masterbatch, used to reduce costs and improve certain properties of products.
Coupling agent: 0.5% -2%, improves the bonding strength between the filler and EVA resin.
Dispersant: 0.5% -2%, helps to evenly disperse fillers in the resin.
It should be noted that the above formula ratios are for reference only. In actual production, adjustments and optimizations will be made based on specific product requirements, raw material properties, and production processes.
عملية الإنتاج
The production process of different types of EVA masterbatch is generally similar, but there may be differences in specific parameters and details. The following is the general production process of EVA masterbatch:
1. تحضير المواد الخام
Accurately select various raw materials such as EVA resin, pigments, flame retardants, foaming agents, fillers, etc. based on the type of masterbatch, and ensure that the quality and purity of the raw materials meet production requirements.
Dry the raw materials to remove moisture and prevent moisture from causing bubbles or other quality issues during processing. For example, EVA resin is usually dried in an oven at 80-100 ℃ for 4-6 hours.
2. خلط المكونات
Accurately weigh various raw materials according to the designed formula ratio. Electronic scales and other measuring devices can be used to ensure the accuracy of ingredients.
Add the weighed raw materials into the high-speed mixer for mixing. The mixing time is generally 5-15 minutes, with a speed of 500-1000 revolutions per minute to ensure thorough and uniform mixing of the raw materials.
3. البثق المنصهر
Add the mixed raw materials into the twin-screw extruder. The temperature setting of the extruder is adjusted according to the melting point and processing performance of EVA resin. It is generally divided into multiple heating zones, and the temperature gradually increases from the inlet to the outlet, usually between 150-200 ℃.
The screw speed is controlled at 100-300 revolutions per minute to fully melt and plasticize the raw materials in the extruder, and further mix them evenly through the shear action of the screw.
During the extrusion process, appropriate additives such as lubricants and antioxidants can be added as needed to improve the processing and usability of the masterbatch.
4. Cooling and granulation
The masterbatch extruded from the extruder is in the form of strips and is cooled by air or water cooling. Air cooling is the use of a fan to blow cold air towards the masterbatch, rapidly cooling it down; Water cooling is to cool the masterbatch through a water tank, which has a faster cooling rate, but it is necessary to pay attention to controlling the water temperature, usually between 20-30 ℃.
The cooled masterbatch is cut into particles of a certain length by a granulator, and the cutting speed and feeding speed of the granulator need to be adjusted according to the diameter and length requirements of the masterbatch to ensure the uniformity and dimensional accuracy of the cutting.
5. Screening and packaging
The cut masterbatch is sieved through a vibrating screen to remove particles that are too large or too small, ensuring that the particle size distribution of the product meets the requirements.
The screened masterbatch is usually packaged in plastic woven bags or paper bags, with each bag weighing 25kg or 50kg depending on customer requirements. Packaged masterbatch should be stored in a dry and ventilated warehouse to avoid moisture and contamination.
In the production process, it is necessary to strictly control the process parameters of each link and conduct regular quality inspections on the products, including appearance, particle size, color fastness, flame retardancy, foaming performance and other indicators, to ensure stable and reliable product quality.
معدات الإنتاج
The equipment for producing EVA masterbatch mainly includes the following types:
معدات الدفعات
Electronic scale: used for precise weighing of various raw materials to ensure the accuracy of ingredient ratios. Depending on the production scale, electronic scales with different ranges and accuracies can be selected, with a general accuracy requirement of ± 0.1g or higher.
High speed mixer: Mix the weighed raw materials thoroughly to ensure even distribution of various components. It has high-speed rotating stirring blades that can achieve efficient mixing in a short period of time, with a mixing capacity typically between 50-500L.
معدات البثق
Twin screw extruder: It is the core equipment for the production of EVA masterbatch. It has two interlocking screws that can efficiently transport, mix, shear, and plasticize materials. The length to diameter ratio of the screw is generally between 20-40, and different specifications such as 35-90mm can be selected according to production capacity. The production capacity ranges from tens of kilograms to hundreds of kilograms per hour.
Melt pump: installed near the discharge port of the extruder, used to accurately control the flow rate of extruded materials, ensure the stability of extrusion volume, and improve the consistency of product quality. The flow range can be selected according to the output of the extruder, generally between 5-50L/min.
Mold: Customize different extrusion molds according to the shape and size requirements of the product. For example, the mold for producing cylindrical EVA masterbatch usually has a mold mouth diameter between 2-6mm, with high precision requirements for shape and size to ensure the appearance quality and size uniformity of the masterbatch.
معدات التبريد
Air cooling system: composed of a fan and cooling pipes, the fan blows cold air towards the extruded masterbatch strip, allowing it to cool rapidly in the air. The air volume of the fan can be adjusted according to the production speed and output, generally ranging from 1000-5000m ³/h.
Water cooling system: including water tank, circulating water pump, and cooling water pipeline, etc. The masterbatch strip is cooled through a water tank, with the water temperature generally controlled at 20-30 ℃. The circulating water pump ensures the circulation of water to maintain the stability of the cooling effect. The length of the sink is usually between 3-10m to meet the cooling needs of the masterbatch at different production speeds.
معدات التحبيب
Granulator: used to cut the cooled masterbatch strips into granules of a specified length. Common types include hot cutting granulators and cold cutting granulators. Hot cutting granulators are suitable for materials with high viscosity, while cold cutting granulators are suitable for general EVA masterbatch. The cutting speed of the granulator can be adjusted between 100-1000 revolutions per minute, and the feeding speed matches the output of the extruder, generally between 1-10m/min.
Screening and packaging equipment
Vibration screen: Screen the cut masterbatch to remove particles that are too large or too small, ensuring that the particle size distribution of the product meets the requirements. The mesh size of the vibrating screen is selected according to the particle size requirements of the product, generally with different specifications such as 20 mesh, 40 mesh, 60 mesh, etc. The screening efficiency can reach over 90%.
Packaging machine: Packaging the screened masterbatch. Common ones include automatic measuring packaging machines, which can automatically complete packaging processes such as measuring, filling, and sealing. The packaging speed varies depending on the packaging specifications, generally between 10-60 bags/hour, and the packaging weight accuracy can be controlled within ± 0.1kg.
In addition, according to specific production needs, some auxiliary equipment may be required, such as raw material storage tanks, feeders, dehumidifiers, crushers, etc., to improve the automation level of production and product quality.
EVA masterbatch extruder
Kerke’s masterbatch extruder can be used to produce EVA masterbatch. Our EVA masterbatch extruder has multiple models to choose from, which can meet different production requirements.
-
آلة البثق اللولبية المزدوجة للمختبر
متى ستحتاج إلى آلة بثق ثنائية اللولب للمختبر؟ إذا كنت ترغب في إجراء تجارب واختبارات...
-
آلة البثق ذات اللولب المزدوج المتوازي
تم تصميم آلة البثق ذات المسمار المزدوج ذات الدوران المتوازي لدينا لتصنيع المركبات والدفعات الرئيسية مع سعة إنتاج تتراوح من...
-
طارد ثلاثي (3 براغي)
آلة البثق ثلاثية البراغي هي تقنية جديدة ذات مزايا عديدة. تُستخدم آلة البثق ثلاثية البراغي بشكل رئيسي...
-
نظام البثق ثنائي المرحلة
تم تصميم نظام بثق الأم والطفل للمواد الخاصة التي لا يمكن معالجتها على مرحلة واحدة من البثق، المرحلة الأولى...
-
خط تصنيع العجنات في بانبوري
تم تصميم آلة العجن والبثق الخاصة بنا لصنع تطبيقات خاصة بسعة إنتاج تتراوح من 30 كجم / ساعة إلى 1000 كجم / ساعة.
-
نظام القطع / نظام التكوير
تحتاج المواد المختلفة إلى نظام قطع مختلف، توفر شركة Kerke جميع أنواع أنظمة القطع، فيما يلي شرح لها…
Related requirements
The extruder is crucial in the production of EVA masterbatch, and the following are the requirements for its performance, screw, heating and cooling system, etc.:
Good plasticizing performance: In the production of EVA masterbatch, different raw materials need to be uniformly plasticized. The extruder should have sufficient plasticizing capacity to quickly and uniformly melt and mix EVA resin and various additives at the set temperature and screw speed, ensuring that the material reaches a good plasticizing state and laying the foundation for subsequent production. For example, for high filling or high viscosity EVA masterbatch formulations, the extruder needs to have stronger plasticizing ability to ensure product quality.
Accurate temperature control: Temperature is a key parameter during the extrusion process. The temperature of each heating zone of the extruder needs to be precisely controlled to adapt to the processing characteristics of EVA resin and the requirements of different formulations. Usually, the temperature control accuracy should reach ± 1 ℃ or even higher in order to avoid problems such as material overheating, decomposition, or poor plasticization caused by temperature fluctuations and ensure stable product performance.
Stable extrusion pressure and flow rate: To ensure the dimensional accuracy and appearance quality of EVA masterbatch, the extruder needs to provide stable extrusion pressure and flow rate. Stable pressure can evenly extrude materials in the mold, avoiding uneven discharge and uneven thickness; A stable flow rate ensures a constant amount of material extruded per unit time, which is beneficial for subsequent cooling and cutting processes. Generally, it is required to control the extrusion pressure fluctuation within ± 5% and the flow fluctuation within ± 3%.
Reasonable screw design: The screw is the core component of the extruder, and its structure and parameters directly affect the conveying, mixing, and plasticizing effects of materials. For the production of EVA masterbatch, the length to diameter ratio, compression ratio and other parameters of the screw need to be optimized and designed according to the specific characteristics of the raw materials and product requirements. The aspect ratio is generally between 25-35, and the compression ratio is between 2-4 to ensure that the material has sufficient residence time and good compression effect inside the screw, achieving sufficient mixing and plasticization. In addition, the thread shape and edge width of the screw can also affect the conveying and shearing performance of the material, and should be selected and adjusted according to the actual situation.
Good mixing and dispersion ability: Various additives such as pigments, flame retardants, and fillers are often added to EVA masterbatch, requiring extrusion machines to have good mixing and dispersion ability to evenly distribute these additives in EVA resin. Through the special design of the screw, such as using mixing elements, kneading blocks, etc., the shear and mixing effects of the material can be enhanced, the dispersion of additives can be improved, and the consistency of product performance can be ensured.
Efficient heating and cooling system: The heating system of the extruder should be able to quickly heat the material to the set temperature and have good insulation performance to reduce heat loss. The cooling system should be able to timely and effectively control the material temperature to prevent local overheating. The response speed of the heating and cooling system should be fast to meet the timely requirements for temperature adjustment in the production process. For example, when the production formula changes and temperature needs to be adjusted, the heating and cooling system should be able to quickly reach the new set value.
High degree of automation: In order to improve production efficiency and product quality stability, extruders should have a high degree of automation. Including automatic control of temperature, screw speed, feed rate and other parameters, as well as safety protection functions such as fault alarm and automatic shutdown. At the same time, it can achieve linkage control with other production equipment, form an automated production line, reduce manual intervention, and improve production consistency and reliability.
طلب
EVA masterbatch has a wide range of applications, mainly including the following fields:
Plastic Modification
Improving flexibility: EVA masterbatch can be used for modifying polyolefin plastics (such as polyethylene and polypropylene) to increase their flexibility and impact resistance. In film production, adding EVA masterbatch can improve the tensile properties and puncture resistance of plastic films, which are widely used in agricultural films, packaging films, and other fields. For example, adding EVA masterbatch to greenhouse films used in agriculture can maintain good flexibility in low temperature environments, prevent cracking, and extend their service life.
Improving processing performance: EVA masterbatch can reduce the melt viscosity of plastics, improve their processing flowability, make plastics easier to form during extrusion, injection molding, and other processing processes, and improve production efficiency and product quality. Adding an appropriate amount of EVA masterbatch during the production of plastic pipes can reduce the phenomenon of melt fracture during extrusion, making the surface of the pipe smoother.
Rubber products
Enhanced weather resistance: EVA masterbatch can be used in rubber products to improve the weather resistance and aging resistance of rubber. Rubber products used outdoors, such as car tires, rubber seals, etc., can resist the erosion of environmental factors such as ultraviolet rays and ozone by adding EVA masterbatch, extending the service life of rubber products.
Reducing hardness: EVA masterbatch can lower the hardness of rubber, increase its softness and elasticity, and provide better comfort and performance for rubber products. For example, adding EVA masterbatch in the production of rubber soles can make the soles softer and more comfortable, while also improving their anti slip performance.
الأسلاك والكابلات
Insulation protection: EVA masterbatch has good insulation properties and can be used as insulation layer and sheath material for wires and cables. It can effectively prevent current leakage, protect wires and cables from external environmental influences, and improve the safety and reliability of wires and cables. In some high demand electronic device cables, using EVA masterbatch as insulation material can meet their requirements for insulation performance and flexibility.
Flame retardant and fire-resistant: Flame retardant EVA masterbatch made by adding flame retardants and other additives can be used to produce wires and cables with flame retardant properties. In the event of a fire, it can delay the spread of the fire, reduce fire losses, and ensure the safety of personnel and equipment. This flame-retardant EVA masterbatch is commonly used for wires and cables in densely populated areas such as buildings and subways.
Hot melt adhesive
Quick bonding: EVA masterbatch is one of the main raw materials for hot melt adhesive, with good bonding performance and fast curing characteristics. EVA hot melt adhesive is widely used in packaging, binding, furniture manufacturing and other industries, which can quickly bond various materials such as paper, wood, plastic, etc., improving production efficiency. For example, in book binding, EVA hot melt adhesive can quickly bond the pages and covers together, and has good durability.
Adapt to different materials: By adjusting the formula and additives of EVA masterbatch, it can be adapted to the bonding requirements of different materials. In the production of shoe materials, EVA hot melt adhesive can be customized according to the material characteristics of the sole and upper, achieving a strong bonding effect while also meeting the usage requirements of shoes in different environments.