EPM masterbatch, also known as ethylene propylene copolymer masterbatch, is a granular concentrate based on ethylene propylene diene monomer (EPM) synthesized from ethylene and propylene as the main monomers, and made by adding carrier resin, fillers, and additives. EPM masterbatch belongs to a type of plastic masterbatch, composed of super constant chemical additives, carrier resins, and dispersants. Its essence is to uniformly attach pigments, additives, etc. to the resin to form aggregates, which are used to simplify the plastic processing flow and stabilize product quality.
Characteristic
1. Excellent weather resistance: EPM masterbatch has excellent weather resistance, high resistance to sunlight, ozone, and wind and rain erosion, and is not prone to aging, cracking, hardening, and brittleness. It can maintain stable performance for a long time and is suitable for outdoor long-term use products.
2. Good chemical corrosion resistance: It has excellent resistance to various chemical substances, such as acids, bases, salt solutions, and some organic solvents. When in contact with these chemicals, its performance is not easily affected and can be used to manufacture products used in chemical corrosion environments.
3. High elasticity and flexibility: With high elasticity and good flexibility, it can maintain elasticity within a large deformation range and quickly restore its original state, making it suitable for manufacturing products that require frequent bending, stretching, or compression, such as seals, shock absorbers, etc.
4. Low softness and smoothness: It can maintain good flexibility and elasticity in low temperature environments, is not easily brittle, and can maintain stable performance over a wide temperature range. It can be used in cold regions or occasions that require low temperature performance.
5. Excellent electrical insulation performance: With good electrical insulation performance, it can be used as an insulation layer and sheath material for wires and cables, effectively preventing current leakage and ensuring the safe operation of electrical equipment and lines.
6. Good processing performance: easy to process and shape, can be made into various shapes of products through various processing methods such as extrusion, injection molding, and compression molding, and has good fluidity during the processing, which can improve production efficiency and reduce processing costs.
7. Environmentally friendly and non-toxic: It is usually environmentally friendly and non-toxic, meets relevant environmental standards and requirements, and can be used in areas that come into contact with the human body or have high environmental requirements, such as medical devices, food packaging, etc.
8. Strong fillability: It can fill a large amount of various fillers, such as calcium carbonate, talc powder, etc., without significantly reducing their performance, it can reduce material costs and improve certain properties of the product, such as hardness and dimensional stability.
Types
EPM is ethylene propylene diene monomer rubber, and usually EPM masterbatch can be divided into the following types according to function and purpose:
Universal masterbatch: It has the basic characteristics of ethylene propylene rubber, such as good weather resistance, ozone resistance, chemical corrosion resistance, etc. It can be widely used in the production of rubber products, such as automotive parts, wire and cable sheaths, seals, etc., to improve the comprehensive performance of products.
High filling masterbatch: A large amount of fillers such as calcium carbonate, talc powder, etc. are added to EPM masterbatch. This type of masterbatch can reduce the cost of rubber products while maintaining certain physical properties, making it suitable for cost sensitive applications such as building waterproofing materials and general industrial rubber products.
Easy to process masterbatch: By designing a special formula and improving the processing technology of EPM, it has better processing performance, such as lower Mooney viscosity and good flowability. This type of masterbatch is convenient for mixing, extrusion, molding and other operations during rubber processing, improving production efficiency. It is suitable for the production of complex shaped rubber products, such as rubber fittings and rubber miscellaneous parts.
Sulfide type masterbatch: According to the different sulfurization methods, it can be divided into peroxide sulfurization type masterbatch and sulfur sulfurization type masterbatch. Peroxide vulcanization masterbatch has the advantages of fast vulcanization speed and good rubber properties, making it suitable for producing high-performance rubber products; Sulfur sulfide masterbatch has the characteristics of low cost and mature vulcanization process, and is widely used in the production of general rubber products.
Functional masterbatch: special functional additives such as anti-aging agent, flame retardant, antistatic agent, etc. are added to EPM masterbatch to give special functions to rubber products. For example, adding anti-aging agent can improve the anti-aging performance of rubber products and extend the service life; Adding flame retardants can make rubber products have flame retardant properties, suitable for occasions with high fire prevention requirements; Adding anti-static agents can eliminate static electricity on the surface of rubber products and prevent the harm caused by static electricity accumulation.
Fórmula
The following is the approximate formula ratio range for different types of EPM masterbatch. The actual formula may vary due to factors such as the manufacturer and product performance requirements:
Universal masterbatch
EPM rubber: 100 parts, is the main component of the masterbatch, providing basic rubber properties.
Zinc oxide: 3-5 parts, used as an active agent to promote sulfurization reaction.
Stearic acid: 1-2 parts, helps improve processing performance and enhance compatibility between rubber and fillers.
Carbon black: 30-60 parts, can enhance the strength, wear resistance, conductivity and other properties of rubber. Different types and particle sizes of carbon black can be selected according to product performance requirements.
Paraffin oil: 10-30 parts, used as a plasticizer to improve the flexibility and processability of rubber.
Vulcanizing agent: 1-2 parts, commonly used include sulfur, etc., which causes cross-linking reaction of rubber, forms a three-dimensional network structure, and improves the performance of rubber.
Accelerator: 1-3 parts, such as dithiocarbamate salts, thiazoles, etc., to accelerate the sulfurization reaction.
High filling type masterbatch
EPM rubber: 60-80 parts, leaving space for the addition of a large amount of fillers while ensuring the basic properties of the rubber.
Zinc oxide: 3-5 parts, with the same function as the universal masterbatch.
Stearic acid: 1-2 parts, improves processing performance and compatibility.
Calcium carbonate: 80-150 parts, as the main filler, can significantly reduce costs while increasing the hardness and dimensional stability of rubber.
Talc powder: 0-50 parts, can be used in combination with calcium carbonate to further increase the filling amount and improve certain properties, such as heat resistance and insulation.
Carbon black: 10-30 parts, used to enhance the performance of rubber appropriately.
Paraffin oil: 10-20 parts, helps to better disperse fillers in rubber and improve processing performance.
Vulcanizing agent: 1-2 parts, determine the specific dosage according to the vulcanization system.
Accelerator: 1-3 parts, used in combination with vulcanizing agent to control the vulcanization rate.
Easy to process masterbatch
EPM rubber: 100 parts, choose EPM rubber varieties with low Mooney viscosity and good flowability.
Zinc oxide: 3-5 parts, promotes sulfurization reaction.
Stearic acid: 1-2 parts, improve processing performance.
Carbon black: 30-50 parts, choose the appropriate carbon black variety and dosage according to product performance requirements.
Paraffin oil: 20-40 parts, increases the flexibility and fluidity of rubber, and reduces processing difficulty.
Sulfurizing agent: 1-2 parts, ensure the sulfurization reaction proceeds normally.
Accelerator: 1-3 parts, choose accelerator with moderate vulcanization speed for easy control during processing.
Processing aids: 1-5 parts, such as lubricants, dispersants, etc., to further improve processing performance and make rubber smoother during mixing, extrusion, molding, and other processes.
Sulfurized masterbatch
Peroxide vulcanized masterbatch: 100 parts EPM rubber; 3-5 parts of zinc oxide; 1-2 parts of stearic acid; 30-60 parts of carbon black; 10-30 parts of paraffin oil; 2-7 parts of peroxide vulcanizing agent, such as DCP (diisopropylbenzene peroxide), etc; 0-3 parts of crosslinking agents, such as TAIC (triallyl isocyanurate), can improve crosslinking efficiency and the performance of vulcanized rubber.
Sulfur vulcanized masterbatch: 100 parts EPM rubber; 3-5 parts of zinc oxide; 1-2 parts of stearic acid; 30-60 parts of carbon black; 10-30 parts of paraffin oil; 1-2 parts of sulfur; 1-3 parts of accelerators, commonly used accelerators include dithiocarbamate salts, thiazoles, etc. Different accelerators have different effects on vulcanization speed and vulcanized rubber properties, and can be selected and compounded according to needs.
Functional masterbatch
Anti aging master batch: based on the general master batch formula, add 1-5 parts of anti-aging agent, such as antioxidant RD, antioxidant 4010NA, etc., which can inhibit the aging of rubber in the long-term use process and extend the service life of the product.
Flame retardant masterbatch: 100 parts EPM rubber; 3-5 parts of zinc oxide; 1-2 parts of stearic acid; Appropriate amount of carbon black (determined according to product performance requirements); 10-30 parts of paraffin oil; 10-30 parts of flame retardant, such as aluminum hydroxide, magnesium hydroxide, decabromodiphenyl ether, etc., can improve the flame retardant performance of rubber and meet the corresponding fire prevention standards.
Antistatic masterbatch: 100 parts EPM rubber; 3-5 parts of zinc oxide; 1-2 parts of stearic acid; Moderate amount of carbon black (generally less than general masterbatch); 10-30 parts of paraffin oil; 1-5 parts of anti-static agents, such as quaternary ammonium salts, sulfonic acid salts, etc., can reduce the surface resistance of rubber and prevent static electricity accumulation.
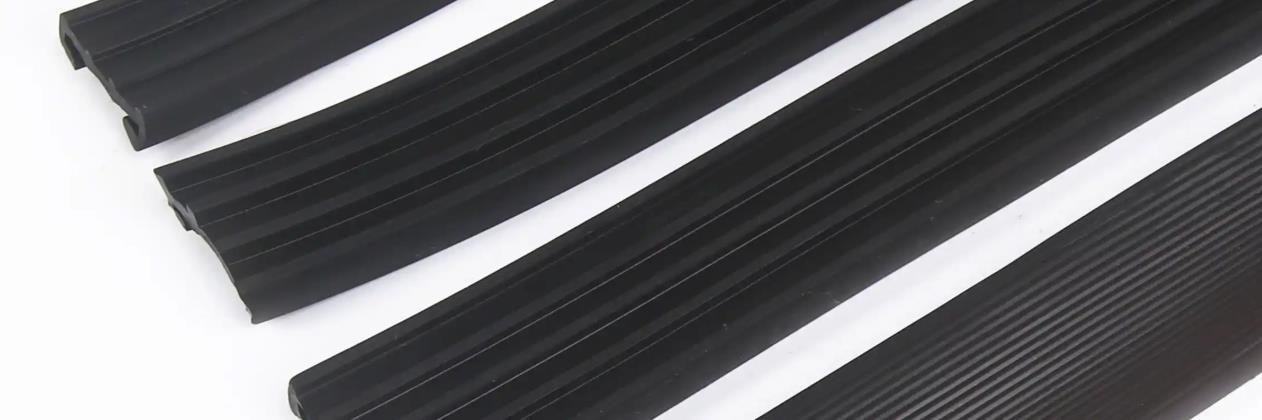
Proceso de producción
The production process of EPM masterbatch usually includes the following main steps:
Preparación de la materia prima
EPM rubber: Select appropriate EPM rubber varieties and grades based on product performance requirements, check their quality and performance indicators to ensure compliance with production requirements.
Additives: Prepare various additives such as zinc oxide, stearic acid, carbon black, paraffin oil, vulcanizing agents, accelerators, functional additives, etc., and accurately weigh them according to the formula requirements.
Mixing
Initial mixing: Put EPM rubber into a mixer or open mill for initial plasticization to give it a certain plasticity and flowability, which facilitates the subsequent mixing of additives.
Add additives: Add zinc oxide, stearic acid, carbon black, paraffin oil and other additives to the mixing equipment in the order of the formula, and mix them thoroughly with the rubber. During the mixing process, it is necessary to control parameters such as temperature, time, and speed to ensure that the additives are evenly dispersed in the rubber. For high filling masterbatch, due to the large amount of filler used, special mixing processes or equipment may be required, such as using a twin-screw extruder for mixing, to improve the dispersion effect of the filler.
Final mixing: Near the end of mixing, add vulcanizing agents and accelerators, and continue mixing for a period of time to evenly distribute the vulcanizing agents and accelerators in the rubber, but be careful to avoid excessive mixing that may cause the vulcanizing agents to react prematurely.
Granulación por extrusión
Extrusion: The mixed rubber material is fed into an extruder, and the extruder’s screw rotates to subject the rubber material to extrusion and shear forces inside the barrel, further mixing and extruding it into strips or granules. The temperature, screw speed, and head pressure of the extruder have a significant impact on the quality and appearance of the product, and need to be adjusted according to the characteristics of the rubber material and product requirements.
Granulation: The extruded rubber strips or granules are granulated by a granulator, usually cooled and shaped by water or air cooling, and then cut into particles of a certain size by a granulator. During the granulation process, it is necessary to control the cutting speed and size of the granules to ensure that the particle size of the mother granules is uniform and consistent.
Package
The produced EPM masterbatch is usually packaged in plastic film bags or woven bags to prevent moisture, contamination, and oxidation of the masterbatch. For some products with high packaging requirements, vacuum packaging or nitrogen filling packaging may be used to extend the storage period of the masterbatch and ensure product quality.
Throughout the entire production process, it is necessary to strictly control the process parameters of each link, such as temperature, time, speed, pressure, etc., and conduct necessary quality inspections, such as appearance inspection, particle size distribution testing, physical performance testing, etc., to ensure that the produced EPM masterbatch meets quality standards and customer requirements. At the same time, attention should be paid to the cleanliness and hygiene of the production environment to prevent impurities from entering the masterbatch and affecting product quality.
Production equipment
The EPM masterbatch production equipment mainly includes equipment for raw material processing, mixing, extrusion granulation, packaging, and other processes. The following is a specific introduction:
1. Internal mixer: used for preliminary mixing of EPM rubber with various additives. By rotating and interacting with the rotor, materials can be fully mixed and plasticized under high temperature and pressure, effectively improving mixing efficiency and quality, and reducing mixing time.
2. Open mill: It can plasticize EPM rubber and also serve as a supplementary mixing equipment after internal mixing. By using two relatively rotating rollers, the rubber material is subjected to shear and compression in the gap between the rollers, further mixing evenly. Parameters such as roller spacing and temperature can also be adjusted to control the mixing effect.
3. Twin screw extruder: suitable for mixing EPM masterbatch with high filling or complex formulations. Two screws mesh and rotate with each other, allowing the material to be fully mixed, dispersed, and transported in the screw groove, with good self-cleaning and mixing effects, which can better handle high filling materials and make the filler more evenly dispersed in the rubber.
4. Single screw extruder: used to extrude the mixed rubber material into strips or granules. The screw rotates inside the barrel, pushing the rubber material forward. Through heating and shearing, the rubber material is further plasticized and homogenized. The extruder head can be replaced with different molds as needed to produce masterbatch of different shapes and sizes.
5. Granulator: Used in conjunction with an extruder to make the extruded rubber strip into granules. Common types include air-cooled granulators and water-cooled granulators. The air-cooled granulator cools the rubber strip with air and then performs granulation; The water-cooled granulator cools and shapes the rubber strip in water before cutting it into pellets, which can produce mother granules with uniform particle size and good appearance.
6. Granulator: Installed on the granulator, it is used to cut the rubber strip into particles of the specified size. The material and design of the cutting tool have a significant impact on the quality of the cut. Sharp cutting tools can ensure a smooth cut and regular particle shape, and the speed and spacing of the cutting tool can be adjusted according to the particle size requirements of the mother particle.
7. Weighing equipment: including electronic scales, ingredient scales, etc., used to accurately weigh various raw materials. High precision weighing equipment can ensure the accuracy of the formula, thereby stabilizing product quality. Electronic scales can quickly and accurately weigh small doses of additives, while ingredient scales can be used for weighing and batching large quantities of raw materials.
8. Packaging equipment: such as automatic packaging machines, can achieve automatic metering, filling, and sealing packaging of masterbatch. It can improve packaging efficiency, reduce manual operation errors, and ensure consistency in packaging quality. According to packaging specifications and requirements, different types of automatic packaging machines can be selected, such as vertical packaging machines, horizontal packaging machines, etc.
9. Conveyor equipment: including belt conveyors, screw conveyors, etc., used to transport raw materials, rubber materials, and finished masterbatch during the production process. Materials can be transported from one process to another, achieving automated production processes, improving production efficiency, and reducing the labor intensity of manual handling.
10. Testing equipment: such as rubber tensile testing machine, hardness tester, particle size analyzer, etc., used to test the physical properties and particle size distribution of EPM masterbatch. The rubber tensile testing machine can test the mechanical properties such as tensile strength and elongation of the masterbatch. The hardness tester is used to measure the hardness of the masterbatch, and the particle size analyzer can accurately analyze the particle size distribution of the masterbatch to ensure that the product quality meets the standard requirements.
EPM masterbatch extruder
Kerke’s masterbatch extruder can be used to produce EPM masterbatch. Our EPM masterbatch extruder has multiple models to choose from, which can meet different production requirements.
-
Extrusora de doble husillo para laboratorio
¿Cuándo necesitará una extrusora de doble husillo de laboratorio? Si desea realizar ensayos y pruebas de...
-
Extrusora de doble husillo paralelo
Nuestra extrusora de doble husillo paralelo corrotante está diseñada para la fabricación de compuestos y...
-
Extrusor triple (3 tornillos)
La extrusora de 3 tornillos es una nueva tecnología que tiene muchas ventajas. La extrusora de triple tornillo se utiliza principalmente...
-
Sistema de extrusión de doble etapa
El sistema de extrusión madre-bebé está diseñado para materiales especiales que no pueden procesarse en una extrusora de una etapa,...
-
Línea de amasado Banbury
Nuestra amasadora + extrusora está diseñada para realizar aplicaciones especiales con una capacidad de producción de 30kg/h a 1000kg/h....
-
Sistema de corte / Sistema de granulación
Diferentes materiales necesitan diferentes sistemas de corte, Kerke ofrece todo tipo de sistemas de corte, aquí está la explicación de...
Related requirements
The extruder plays a key role in the production of EPM masterbatch, and the following are some requirements for the extruder:
Screw design
Length to diameter ratio: Generally, a larger length to diameter ratio is required, usually between 20-30. A longer screw can provide a longer material conveying and mixing path, allowing EPM rubber to mix evenly with additives, while also facilitating material plasticization and exhaust.
Groove depth: The groove depth should be designed according to the formula and production process of EPM masterbatch. For highly filled EPM masterbatch, deeper screw grooves are required to accommodate more materials and ensure that the filler can be evenly dispersed in the rubber matrix; For formulas with low filling or high shear force requirements, the depth of the screw groove can be appropriately reduced to increase the shear effect on the material and improve the mixing effect.
Screw structure: Adopting a gradient or mutation type screw structure. Gradient screw is suitable for the production of most EPM masterbatch, which can gradually compress and shear the material in the screw, smoothly achieving the transition from solid to melt; Mutant screws are more suitable for some special EPM masterbatch, such as formulations containing a large amount of low melting point additives, which can achieve rapid plasticization of materials in a shorter distance.
Mixing and dispersing ability
Shear element: The screw of the extruder should be equipped with appropriate shear elements, such as kneading blocks, toothed discs, etc. These shearing elements can generate strong shearing and stretching effects, fully mixing EPM rubber with additives, dispersing and uniformly dispersing aggregated additive particles in the rubber matrix, improving the quality and performance uniformity of the masterbatch.
Mixing section design: Set up a dedicated mixing section to further enhance the mixing effect of materials by changing the structure of the screw or installing a special mixing device on the barrel. For example, using pin screws, static mixers, etc., can create complex flow patterns of materials in the mixing section, increase the interaction between materials, and improve the uniformity of mixing.
Temperature control
Heating method: Equipped with an efficient and uniform heating system, commonly used heating methods include electric heating, thermal oil heating, etc. The electric heating method has the advantages of fast heating speed and precise temperature control; Heating with thermal oil can provide a more uniform temperature distribution, making it suitable for large extruders or applications that require high temperature uniformity. The heating device should be able to quickly heat the screw and barrel to the set temperature and maintain temperature stability during the production process.
Cooling system: Equipped with a good cooling system to prevent material degradation or performance changes due to overheating during extrusion. Cooling systems usually use water cooling or air cooling methods to cool screws and barrels through cooling water pipes or fans. The cooling system should be able to automatically adjust the cooling intensity according to the temperature of the material, ensuring that the material is extruded within the appropriate temperature range.
Temperature control accuracy: High temperature control accuracy is required, generally controlled within ± 2 ℃. Accurate temperature control is crucial for ensuring the quality stability of EPM masterbatch. Excessive or insufficient temperature can affect the plasticizing effect of rubber, the dispersibility of additives, and the physical properties of masterbatch.
Pressure control
Stable head pressure: Being able to maintain a stable head pressure is crucial for ensuring the dimensional accuracy and appearance quality of extruded products. A stable head pressure can make the extruded masterbatch have a regular shape and uniform size, avoiding defects such as uneven thickness and bubbles. By adjusting parameters such as screw speed, barrel temperature, and die size, the head pressure can be controlled within an appropriate range.
Pressure regulation range: It has a wide pressure regulation range to meet the requirements of different formulas and production processes. For example, in the production of high filling EPM masterbatch, higher pressure is required to push the material through the mouth mold; When producing low viscosity or low filling masterbatch, lower pressure is required. The extruder should be able to flexibly adjust the pressure according to the actual production situation to ensure smooth production.
Production volume and efficiency
Production capacity: Select extruders with appropriate production capacity based on production scale and market demand. Generally speaking, the output of the extruder should meet the design requirements of the production line and be able to produce a sufficient quantity of EPM masterbatch within the specified time. At the same time, the extruder should have a certain production potential in order to increase the output appropriately when needed.
Automation level: It has a high degree of automation, such as using advanced control systems to achieve automatic adjustment and monitoring of parameters such as screw speed, temperature, and pressure. Highly automated extruders can reduce manual operation errors, improve production efficiency and product quality stability, and also facilitate the management and optimization of the production process.
Material and corrosion resistance
Screw and barrel material: Screw and barrel are usually made of high-strength, wear-resistant, and corrosion-resistant alloy steel materials, such as 38CrMoAlA. These materials have good wear resistance and corrosion resistance, and can withstand the high temperature, high pressure, and shear force of EPM rubber and additives during the extrusion process, extending the service life of the equipment. At the same time, in order to improve the surface hardness and corrosion resistance of screws and barrels, surface treatment processes such as nitriding and hard chromium plating can also be carried out.
Anti corrosion measures: Due to the possible use of corrosive additives such as certain accelerators, anti-aging agents, etc. in the production of EPM masterbatch, corresponding anti-corrosion measures should be taken for the barrel, head, feed inlet, and other parts of the extruder. For example, corrosion-resistant alloy liners are lined on the inner wall of the barrel, and corrosion-resistant coatings or materials are used at the head and feed inlet to prevent equipment from being corroded and affecting normal production and product quality.
Aplicación
EPM masterbatch is an important polymer material with wide applications in multiple fields. The following are some of the main application aspects:
Rubber products
Tire: EPM masterbatch can be used to manufacture components such as sidewall and inner lining of tires. It has good aging resistance, ozone resistance, and chemical corrosion resistance, which can improve the service life and safety of tires. Meanwhile, the high elasticity and low rolling resistance characteristics of EPM masterbatch help reduce fuel consumption and carbon dioxide emissions of vehicles.
Rubber hose: EPM masterbatch can be used as one of the main raw materials in the production of rubber hoses. It can make the rubber hose have excellent oil resistance, water resistance, and high and low temperature resistance, suitable for various working environments, such as fuel pipes for automotive engines, cooling water pipes, and hydraulic hoses in the industrial field.
Seals: EPM masterbatch is commonly used to manufacture various seals, such as oil seals and gaskets for automotive engines, as well as sealing rings in industrial equipment. Its good elasticity and sealing performance can effectively prevent the leakage of liquids and gases, ensuring the normal operation of the equipment.
Plastic Modification
Improving toughness: Adding EPM masterbatch to plastics can significantly enhance their toughness and impact resistance. For example, adding an appropriate amount of EPM masterbatch to polypropylene (PP) plastic can significantly improve its low-temperature impact resistance and expand its application range in cold regions and areas with high toughness requirements.
Improving processing performance: EPM masterbatch can reduce the melt viscosity of plastics, improve their processing flowability, make plastics smoother in extrusion, injection molding and other processing processes, reduce processing defects, and improve production efficiency and product quality. Meanwhile, it can also improve the surface glossiness and appearance quality of plastics.
Wire and cable
Insulation layer: EPM masterbatch has good electrical insulation performance, water resistance, and aging resistance, and is one of the ideal materials for manufacturing insulation layers for wires and cables. It can effectively prevent current leakage and external factors from corroding wires and cables, ensuring the safe and reliable operation of wires and cables.
Sheath: Adding EPM masterbatch to the sheath material of wire and cable can improve the mechanical strength, wear resistance, and chemical corrosion resistance of the sheath, protect the conductors and insulation layers inside the wire and cable from external mechanical damage and chemical substances, and extend the service life of the wire and cable.
Other areas
Building materials: EPM masterbatch can be used to produce waterproofing membranes, sealants, and other materials for construction. Its excellent weather resistance and waterproof performance can effectively prevent buildings from being eroded by rainwater, moisture, etc., improving the waterproof performance and durability of buildings.
Medical devices: Due to the excellent biocompatibility and chemical corrosion resistance of EPM masterbatch, it can be used to manufacture some medical device components, such as medical catheters, seals, etc. It can meet the strict requirements of material safety and reliability for medical devices, ensuring the quality and safe use of medical devices.
Shoe material: In the production of shoe materials, EPM masterbatch can be used to manufacture components such as shoe soles and insoles. It can make the sole have good elasticity, wear resistance, and anti slip performance, improving the comfort and service life of the shoes.