Smooth masterbatch is a functional masterbatch based on polymer materials, made by adding lubricants, anti adhesion agents and other additives, widely used in the field of plastic processing.
Characteristic
Smooth masterbatch is a functional masterbatch widely used in plastic processing, with the following characteristics:
Improve surface performance
Reduce friction coefficient: It can effectively reduce the friction coefficient on the surface of plastic products, making the surface of the products smoother and improving their tactile and operational feel during use. For example, adding smooth masterbatch to plastic film can reduce the friction coefficient between films, facilitate the winding, cutting, and use of films, and reduce adhesion between films.
Improving surface glossiness: It can improve the surface smoothness of plastic products, giving them better glossiness and appearance quality. In the production of some plastic pipes and profiles, adding smooth masterbatch can make the surface of the product smoother and smoother, enhancing the visual effect and grade of the product.
Enhance processing performance
Promote melt flow: During plastic processing, smooth masterbatch can promote the flow of plastic melt, reduce the viscosity of the melt, and make it easier for plastic to form in the mold. This helps to improve processing efficiency, reduce energy consumption during the processing, and also facilitates the production of plastic products with high dimensional accuracy and good surface quality.
Reduce extrusion swelling: It can effectively reduce the swelling phenomenon of plastic during the extrusion process, make the size of extruded products more stable, and improve the molding accuracy of products. For some plastic products that require high dimensional accuracy, such as plastic pipes, cable sheaths, etc., the application of smooth masterbatch can significantly improve the quality and qualification rate of the products.
Stable product quality
Uniform dispersibility: Smooth masterbatch has good dispersibility in plastic matrix, which can be evenly distributed in plastic products, ensuring the consistency and stability of product performance. Whether in large-scale or small-scale production, it can be ensured that each product has the same smoothness and surface quality.
Migration resistance: It has good migration resistance, and during the use of plastic products, it will not migrate to the surface of the product in large quantities due to long-term contact or environmental factors, resulting in decreased product performance or surface sticking problems. This enables plastic products to maintain stable smoothness and appearance quality during long-term use.
Environmental protection and safety
Non toxic and odorless: Most smooth masterbatch is made from non-toxic and odorless raw materials, which comply with relevant environmental and hygiene standards. It can be used in fields such as food packaging and medical devices that require high safety requirements. This ensures that plastic products will not pose a threat to human health and the environment during use.
Recyclability: does not affect the recycling and reuse performance of plastic products. After plastic products are discarded, plastics containing smooth masterbatch can still be recycled and processed to make new plastic products, which is beneficial for saving resources and protecting the environment.
Types
Smooth masterbatch can be classified into different types based on carrier resin, lubricant type, and application field, as follows:
Classified by carrier resin
Polyethylene (PE) Smooth Masterbatch: Made from polyethylene as the carrier resin and additives such as lubricants through special processing technology. Due to the excellent chemical stability, water resistance, and processability of polyethylene, this type of masterbatch has excellent dispersibility and compatibility in polyethylene plastic products, which can effectively improve the surface smoothness of polyethylene films, pipes, injection molded products, etc.
Polypropylene (PP) Smooth Masterbatch: The carrier resin is polypropylene, and the formula is designed based on the characteristics of polypropylene material. In the processing of polypropylene plastic products, such as polypropylene films, fibers, injection molded parts, etc., it can significantly reduce their surface friction coefficient, improve the smoothness and feel of the product, while not affecting the physical and mechanical properties of polypropylene itself.
Other carrier resin slip masterbatch: In addition to common polyethylene and polypropylene carriers, there are also slip masterbatch based on polystyrene (PS), polyvinyl chloride (PVC), polyester (PET) and other carrier resins to meet the requirements of different resin material products for slip performance. For example, the application of PET smooth masterbatch in products such as polyester films and preforms can improve their surface properties, increase production efficiency and product quality.
Classified by type of lubricant
Fatty acid amide based slip masterbatch: This is the most common type of slip masterbatch, mainly containing fatty acid amide based slip agents such as oleic acid amide and erucic acid amide. This type of lubricant has a good smoothing effect and can form a uniform lubricating film on the surface of plastic products, effectively reducing the friction coefficient and improving surface glossiness. Meanwhile, fatty acid amide based lubricants also have certain anti-static properties, which can reduce dust adsorption on the surface of plastic products.
Organic silicone based slip masterbatch: using organic silicone compounds as the main slip agent, such as polydimethylsiloxane. Organic silicone lubricants have extremely low surface tension, which can endow plastic products with excellent smoothness and waterproofing properties. In addition, silicone based slip masterbatch can improve the heat resistance and weather resistance of plastic products, enabling them to maintain stable slip effects under different environmental conditions.
Inorganic smooth masterbatch: containing inorganic lubricants such as talc powder, diatomaceous earth, and silica. Inorganic slip agents have good wear resistance and high temperature resistance, and can form a microscopic smooth structure on the surface of plastic products, thereby improving their slip performance. This type of smooth masterbatch is usually used for plastic products that require high wear resistance and heat resistance, such as engineering plastics, rubber products, etc.
Classified by application field
Thin film specific smooth masterbatch: Optimized for the production and application characteristics of plastic films, it can form a uniform smooth layer on the surface of the film, effectively prevent film adhesion, and improve the opening and winding performance of the film. Widely used in agricultural film, packaging film, electronic film and other fields.
Special Smooth Masterbatch for Injection Molding Products: During the injection molding process, it can improve the fluidity of the plastic melt, making the product easier to demold, while also increasing the smoothness and smoothness of the product surface, reducing surface defects. Suitable for various injection molded plastic products, such as plastic containers, toys, automotive parts, etc.
Fiber specific smooth masterbatch: used in fiber production, it can reduce the friction coefficient between fibers, improve the spinnability and processing performance of fibers, and make fibers have good softness and smooth hand feel. Commonly used in the production of synthetic fibers such as polyester fibers, polypropylene fibers, nylon fibers, etc.
Fórmula
The formula ratio of the smooth masterbatch may vary depending on the type, application scenario, and performance requirements. The following are the approximate formula ratios for some common types of smooth masterbatch:
Fatty acid amide based smooth masterbatch (with PE as the carrier)
Fatty acid amides (such as oleic acid amides, erucic acid amides): 5% -20%
As the main smoothing component, if the content is too low, the smoothing effect will not be significant, and if it is too high, it may cause frost spraying on the surface of the product.
Antioxidant: 0.1% -0.5%
Prevent the oxidation and deterioration of masterbatch during processing and storage, and extend the service life of masterbatch.
Dispersant: 0.5% -2%
Help the lubricant to be evenly dispersed in the carrier resin, improving the stability and consistency of the masterbatch.
Polyethylene (PE) carrier resin: 77.5% -94.4%
Carrying lubricants and other additives to ensure uniform addition to plastic products, while ensuring compatibility between the masterbatch and the matrix resin.
Organic silicone smooth masterbatch (using PP as the carrier)
Organic silicon compounds (such as polydimethylsiloxane): 10% -30%
It is a key component that provides excellent smoothness and waterproofing performance, and its content is adjusted according to the required smoothness level and product performance requirements.
Anti adhesive agent: 1% -5%
Prevent plastic products from sticking to each other after molding, and work together with silicone lubricants to improve the performance of the products.
Light stabilizer: 0.2% -1%
Improve the weather resistance of masterbatch and products, prevent organic silicon compounds from degrading under light, and affect the smoothness effect.
Polypropylene (PP) carrier resin: 64% -88.8%
As a carrier, it ensures the uniform dispersion of organosilicon compounds in plastic products while endowing the masterbatch with good processing properties.
Inorganic smooth masterbatch (using PET as the carrier)
Inorganic lubricants (such as talcum powder, diatomaceous earth, etc.): 20% -50%
Provide wear and high temperature resistance, increase the micro smoothness of the product surface, and have a high content to meet the specific performance requirements of the product.
Coupling agent: 0.5% -2%
Improve the adhesion between inorganic lubricants and PET carrier resin, and enhance the performance and stability of the masterbatch.
Lubricant: 0.5% -3%
Helps to reduce friction during processing, improve the dispersion of inorganic lubricants in the carrier resin, and enhance the surface quality of the product.
Polyester (PET) carrier resin: 45% -79%
Carrying inorganic lubricants to ensure compatibility and dispersion of masterbatch in PET products, while not affecting the performance of PET itself.
The above formula ratios are for general reference only. In actual production, manufacturers will optimize and adjust them based on specific product requirements, processing techniques, and cost factors.
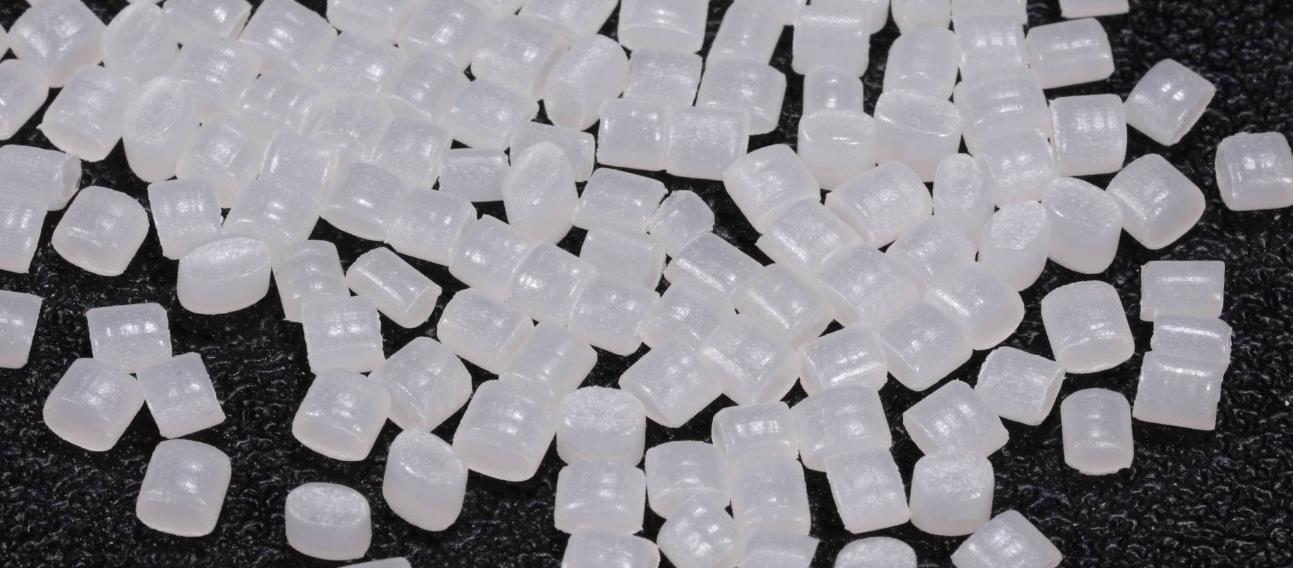
Proceso de producción
The production process of smooth masterbatch usually includes steps such as raw material preparation, mixing, melt extrusion, cooling granulation, packaging, etc. The following is a specific introduction:
1. Preparación de la materia prima
Choose carrier resin: Based on the application field and performance requirements of the smooth masterbatch, select the appropriate carrier resin, such as polyethylene, polypropylene, polyester, etc. The carrier resin should have good processability and compatibility with lubricants.
Select a lubricant: Based on the desired lubricant effect and product characteristics, choose a lubricant such as fatty acid amide, organosilicon, or inorganic. At the same time, appropriate auxiliary additives such as antioxidants, dispersants, light stabilizers, etc. can be added as needed to improve the performance and stability of the masterbatch.
Raw material drying: For materials with strong moisture absorption, such as polyester resin, drying treatment is required to remove moisture and prevent problems such as bubbles or degradation during processing, which may affect the quality of the masterbatch.
2. Mezcla
Initial mixing: The carrier resin, lubricant, and various additives are added to a high-speed mixer in a certain formula ratio for initial mixing. By high-speed stirring, various raw materials can achieve initial uniform dispersion in a short period of time, preparing for subsequent melt extrusion.
Mixing: After initial mixing, the material is further mixed and plasticized in the mixing machine. The internal mixer has strong shearing and mixing effects, which can make additives such as lubricants more evenly dispersed in the carrier resin, and improve the performance stability of the masterbatch.
3. Melt extrusion
Extruder plasticization: Adding the mixed material into a twin-screw extruder. Twin screw extruders have good conveying, mixing, and plasticizing capabilities, which can fully melt and plasticize materials under heating and screw shearing. During the extrusion process, it is necessary to control the temperature, speed, and other process parameters of the extruder to ensure the plasticization quality of the material and the dispersion effect of the lubricant.
Filtering: In order to ensure the quality of the masterbatch, filtering devices such as filters or melt filters are usually installed during the extrusion process to remove impurities and insufficiently dispersed aggregates from the material, improve the purity and appearance quality of the masterbatch.
4. Cooling granulation
Water cooling or air cooling: The molten material extruded from the extruder is formed into strips or filaments through the die head, and then enters a cooling water tank or air cooling device for cooling. The water cooling method has a fast cooling speed and can quickly shape the masterbatch, but it may result in a higher surface moisture content of the masterbatch; The air cooling method is relatively mild and can avoid residual moisture, but the cooling efficiency is lower.
Granulation: The cooled material is cut into granules of a certain length by a granulator, and the cutting speed and cutting method of the granulator will affect the particle size and shape of the mother granules. Generally speaking, it is required that the particle size of the masterbatch be uniform and the shape be regular to ensure dispersion and processing performance during use.
5. Embalaje
Screening: After granulation, the mother granules are passed through a screening device to remove particles that are too large or too small, ensuring the consistency of the product’s particle size. At the same time, metal impurities that may be mixed in can be removed through magnetic separation and other devices.
Packaging: Fill the smooth masterbatch that meets the quality requirements into a packaging bag or container and seal it for packaging. During the packaging process, attention should be paid to preventing moisture and contamination of the masterbatch to ensure the quality and storage stability of the product.
In the actual production process, different manufacturers may make appropriate adjustments and optimizations to the production process based on their own equipment conditions, product requirements, and production experience, in order to produce smooth masterbatch products with excellent performance and stable quality.
Production equipment
The production of smooth masterbatch requires multiple devices to work together to complete a series of processes from raw material processing to finished product packaging. The following are the main production equipment:
1. Equipo de ingredientes
Electronic scale: used for precise weighing of various raw materials, such as carrier resins, lubricants, additives, etc. According to the production scale and accuracy requirements, electronic scales with different ranges and accuracies can be selected to ensure the accuracy of ingredient ratios.
Automatic batching system: In large-scale production, automatic batching systems are often used, which can automatically complete the measurement and batching process of various raw materials according to preset formulas, improve batching efficiency and accuracy, and reduce manual operation errors.
2. Hybrid equipment
High speed mixer: preliminary mixing of various raw materials, and achieving uniform mixing of materials in a short period of time through high-speed rotating stirring blades. It has the characteristics of fast mixing speed and good mixing effect, which can preliminarily disperse additives such as lubricants in the carrier resin.
Mixing machine: Further mixing and plasticizing the initially mixed materials, through strong shearing and mixing effects, to fully integrate the lubricant with the carrier resin, improve the uniformity and stability of the materials, and prepare for subsequent extrusion processing.
3. Extrusion equipment
Twin screw extruder: It is one of the key equipment for producing smooth masterbatch. It has good conveying, mixing, and plasticizing capabilities, which can fully melt and plasticize materials under heating and screw shearing, while uniformly dispersing additives such as lubricants in the carrier resin. By adjusting parameters such as screw speed and temperature, the extrusion speed and plasticization quality of materials can be controlled.
Extruder auxiliary equipment: including head mold, filter screen replacement device, etc. The head mold is used to shape the extruded molten material into the desired shape, such as strip or filament; The filter replacement device can promptly replace clogged filters during the extrusion process, ensuring the continuity of the extrusion process and the purity of the material.
4. Cooling equipment
Cooling water tank: using water cooling method to quickly cool and shape extruded strip or filamentous materials. The length, water temperature, and water flow rate of the cooling water tank can be adjusted according to the characteristics of the material and production speed to ensure that the material can be quickly cooled to the appropriate temperature for subsequent granulation operations.
Air cooling device: For materials that are not suitable for water cooling or have high requirements for surface moisture, air cooling devices can be used for cooling. The air cooling device removes heat from the surface of the material by forcing air flow, gradually cooling and shaping the material. Its advantage is that it does not introduce moisture, but the cooling rate is relatively slow, making it suitable for situations where cooling rate requirements are not high.
5. Granulation equipment
Granulator: Cut the cooled material into particles of a certain length. According to different production needs, it can be divided into hot cutting granulator and cold cutting granulator. Hot cutting granulator is used to cut materials in a molten state and is suitable for materials with high viscosity; The cold granulator is a commonly used granulation equipment in the production of smooth masterbatch, which cuts the material after cooling and shaping, and produces particles with regular shapes and uniform sizes.
6. Screening equipment
Vibration screen: used to screen the smooth masterbatch after granulation, remove particles that are too large or too small, and ensure the consistency of product particle size. The vibrating screen can select different mesh sizes according to different particle size requirements, and through the action of the vibration motor, the material is fully vibrated on the screen to achieve particle classification and screening.
7. Packaging equipment
Automatic packaging machine: Automatically package the screened smooth masterbatch according to a certain weight. Automatic packaging machines have the characteristics of accurate measurement and fast packaging speed. They can be adjusted according to the packaging specifications of the product to complete packaging processes such as material filling and sealing, improving packaging efficiency and quality. At the same time, some packaging machines also have functions such as labeling and coding, which facilitate product identification and traceability.
In addition, in order to ensure the normal operation of production equipment and the stability of product quality, it is necessary to equip some auxiliary equipment, such as air compressors, dehumidifiers, central feeding systems, etc. These devices together form the production equipment system for smooth masterbatch, and different manufacturers can make reasonable choices and configurations based on their own production scale, product requirements, and process characteristics.
Smooth masterbatch extruder
Kerke’s masterbatch extruder can be used to produce smooth masterbatch. Our smooth masterbatch extruder has multiple models to choose from, which can meet different production requirements.
-
Extrusora de doble husillo para laboratorio
¿Cuándo necesitará una extrusora de doble husillo de laboratorio? Si desea realizar ensayos y pruebas de...
-
Extrusora de doble husillo paralelo
Nuestra extrusora de doble husillo paralelo corrotante está diseñada para la fabricación de compuestos y...
-
Extrusor triple (3 tornillos)
La extrusora de 3 tornillos es una nueva tecnología que tiene muchas ventajas. La extrusora de triple tornillo se utiliza principalmente...
-
Sistema de extrusión de doble etapa
El sistema de extrusión madre-bebé está diseñado para materiales especiales que no pueden procesarse en una extrusora de una etapa,...
-
Línea de amasado Banbury
Nuestra amasadora + extrusora está diseñada para realizar aplicaciones especiales con una capacidad de producción de 30kg/h a 1000kg/h....
-
Sistema de corte / Sistema de granulación
Diferentes materiales necesitan diferentes sistemas de corte, Kerke ofrece todo tipo de sistemas de corte, aquí está la explicación de...
Related requirements
The parameter setting of the extruder is crucial in producing smooth masterbatch, as it directly affects the quality and production efficiency of the product. Here are some common extruder parameter settings:
1. Temperature setting
Feeding section: The temperature is generally set at 150-180 ℃. This section mainly transports the material into the extruder, and the temperature should not be too high, otherwise it may cause premature melting of the material and affect its normal transportation.
Compression section: The temperature is usually between 180-220 ℃. As the screw rotates, the material is gradually compressed in this section, and the temperature gradually increases, causing the material to start melting and initially mixing. Higher temperatures help improve the plasticizing effect of the material.
Measurement section: The temperature is generally controlled between 220-250 ℃. In the measuring section, the material needs to reach a fully melted state and ensure temperature uniformity for accurate measurement and extrusion. For some special carrier resins or lubricants, it may be necessary to fine tune the temperature according to their characteristics.
Head: The temperature is generally set at 230-260 ℃. The temperature of the machine head directly affects the forming quality of the extruded material. If the temperature is too high, it may cause excessive expansion and rough surface of the material during extrusion; If the temperature is too low, problems such as difficulty in material extrusion and cracks on the surface of the product may occur.
2. Screw speed
Usually between 100-300 revolutions per minute. Lower rotational speed is suitable for situations where shear force is not high, material viscosity is high, or degradation is easy. It can reduce the residence time of materials in the extruder and lower the risk of degradation. Higher rotational speeds are suitable for situations that require high shear forces to disperse lubricants and improve production efficiency, but excessive rotational speeds may cause material overheating, degradation, and increase equipment wear. In actual production, the appropriate screw speed should be selected based on the characteristics of the material, formula, and performance of the extruder, and optimized through experiments.
3. Back pressure
The back pressure is generally controlled between 0.5-3MPa. Appropriate back pressure can improve the density and plasticization quality of materials, allowing additives such as lubricants to be better dispersed in the carrier resin. However, excessive back pressure can increase the load on the extruder, reduce production efficiency, and may also lead to material overheating and degradation; If the back pressure is too low, good plasticization and mixing effects cannot be achieved. In actual production, back pressure can be controlled by adjusting the throttle valve of the extruder or using variable frequency motors.
4. Feeding speed
The feeding speed should match the screw speed and the production capacity of the extruder. Generally speaking, the feeding speed should ensure that the material can enter the extruder evenly and continuously, avoiding situations of material breakage or insufficient feeding. Usually, the feeding speed is set within a certain range based on the specifications and production requirements of the extruder, such as 5-20 kilograms per hour. During the production process, the feeding speed can be precisely controlled by adjusting the speed of the feeder or using an automatic feeding system.
The above parameters are only a rough range, and in actual production, they need to be flexibly adjusted and optimized according to specific raw material formulas, equipment models, and product quality requirements. Before starting up, the extruder should be preheated to ensure that the temperature of each section reaches the set value and stabilizes before proceeding with feeding production. At the same time, close attention should be paid to the operation status and product quality of the extruder during the production process, and the parameters should be adjusted in a timely manner to ensure the production of stable and smooth masterbatch products.
Aplicación
Smooth masterbatch has the functions of improving the surface smoothness of plastic products and reducing the friction coefficient, so it has a wide range of applications in multiple fields. The following are some main application aspects:
Plastic film industry
Improving smoothness: Adding smoothness masterbatch in the production of plastic film can significantly reduce the friction coefficient of the film surface, thereby improving the smoothness and ease of opening of the film. This is very important for the high-speed automatic packaging, printing and other subsequent processing of films, which can effectively improve production efficiency and reduce adhesion and damage between films.
Improving anti adhesion: Smooth masterbatch can form a uniform lubricating film on the surface of the film, preventing the film from being difficult to separate due to mutual adhesion during storage and use, especially suitable for fields such as food packaging and agricultural films, which can ensure the performance and packaging effect of the film.
Plastic pipe industry
Reduce frictional resistance: Adding smooth masterbatch in the extrusion production of plastic pipes can reduce the friction coefficient of the inner and outer surfaces of the pipes, making them easier to be dragged during the laying process, reducing frictional resistance with the ground or other objects, lowering construction difficulty and damage to the pipe surface.
Improving surface quality: Smooth masterbatch helps to improve the surface smoothness of pipes, making the pipe surface smoother and smoother, reducing fluid resistance caused by surface roughness, and improving the fluid transport efficiency of pipes. It is especially suitable for fields such as water supply and drainage pipes, gas transportation pipes, etc. that require high surface quality.
Injection molding industry
Easy demolding: During the injection molding process, the smooth masterbatch can reduce the friction between the plastic product and the mold, making it easier for the product to be removed from the mold, reducing demolding time and force, improving injection molding production efficiency, and also reducing the incidence of surface scratches, deformations, and other defects caused by difficult demolding.
Improving surface performance: For injection molded products that require good surface feel and appearance quality, such as plastic toys, home appliance shells, etc., smooth masterbatch can make the surface of the product smoother and more delicate, improve the texture and touch of the product, and enhance its market competitiveness.
Fiber industry
Reducing inter fiber friction: In the production of synthetic fibers, adding smooth masterbatch can reduce the friction coefficient between fibers, prevent entanglement, fuzz and other phenomena during processing, and improve the spinnability and processing performance of fibers.
Improving fiber feel: Fibers treated with smooth masterbatch have good smoothness on their surface, giving fiber products such as fabrics and non-woven fabrics a soft and smooth feel, improving the comfort and performance of the product.