LLDPE masterbatch, also known as linear low-density polyethylene masterbatch, is a granular raw material mainly composed of linear low-density polyethylene (LLDPE). LLDPE masterbatch is a non-toxic, odorless, and milky white particle with a density of 0.918~0.935g/cm ³. Compared with LDPE, it has higher softening temperature and melting temperature, stronger strength, better toughness, higher rigidity, better heat and cold resistance, as well as good resistance to environmental stress cracking, impact strength, tear strength, and can resist acid, alkali, organic solvents, etc.
Types
LLDPE (linear low-density polyethylene) masterbatch can be divided into the following main types based on their functions and additives:
Universal LLDPE masterbatch
This is the most common type with good overall performance. It is made from LLDPE as the base resin, with the addition of appropriate lubricants, antioxidants and other additives, and processed into a finished product.
It has excellent tensile performance, tear resistance, and puncture resistance, as well as good flexibility and transparency.
Widely used in various fields such as plastic films, pipes, injection molded products, etc., such as agricultural films, packaging films, plastic pipes, etc.
Filled LLDPE masterbatch
Add a certain amount of inorganic fillers such as calcium carbonate, talcum powder, kaolin, etc. to LLDPE masterbatch to make filled LLDPE masterbatch.
Adding fillers can reduce production costs and improve certain properties of plastic products, such as increasing hardness, rigidity, heat resistance, etc.
Commonly used in the production of plastic products that are cost sensitive and have certain performance requirements, such as plastic turnover boxes, garbage bins, and plastic pipes for construction.
Functional LLDPE masterbatch
Anti aging masterbatch: high efficiency anti-aging additives such as light stabilizer and antioxidant are added, which can effectively improve the weather resistance and anti-aging performance of plastic products, prevent them from discoloration, cracking, embrittlement and other phenomena during long-term outdoor use, and extend the service life. Commonly used in agricultural films, shade nets, outdoor plastic products, etc.
Antibacterial masterbatch: Adding antibacterial agents to give plastic products antibacterial and bactericidal functions. It can inhibit the growth and reproduction of microorganisms such as bacteria and molds, prevent the growth of bacteria on the surface of products, and maintain cleanliness and hygiene. Commonly used in fields such as food packaging, medical devices, and hygiene products.
Anti static masterbatch: Adding anti-static agents can reduce the surface resistance of plastic products, making them have good anti-static properties, and prevent plastic products from adsorbing dust, generating sparks, and other problems due to static electricity accumulation during production, storage, and use. Widely used in electronic and electrical product packaging, plastic film, plastic containers and other fields.
Color matching LLDPE masterbatch
According to customer requirements, various pigments or color powders are mixed with LLDPE resin to create color matching masterbatch of specific colors.
It has good dispersibility and coloring power, which can make plastic products achieve uniform and bright colors.
Widely used in various plastic product fields that require coloring, such as plastic films, pipes, injection molded products, fibers, etc., to meet different customers’ needs for product appearance color.
Formula ratio
The formula ratio of LLDPE masterbatch may vary depending on the type of masterbatch and specific application requirements. Here are some examples of approximate formula ratios for common types of LLDPE masterbatch:
Universal LLDPE masterbatch
LLDPE resin: 80% -90%
Slippery agent: 0.5% -2%
Antioxidant: 0.1% -0.5%
Other additives (such as dispersants, etc.): 0.5% -2%
Filler (optional): 5% -15%
Filled LLDPE masterbatch
LLDPE resin: 40% -70%
Inorganic fillers (such as calcium carbonate, talc powder, etc.): 30% -60%
Coupling agent: 0.5% -2%
Antioxidant: 0.1% -0.5%
Other additives (such as lubricants, etc.): 0.5% -2%
Anti-aging masterbatch
LLDPE resin: 70% -85%
Light stabilizer: 2% -5%
Antioxidant: 1% -3%
Other additives (such as dispersants, etc.): 0.5% -2%
Filler (optional): 10% -20%
Antibacterial masterbatch
LLDPE resin: 80% -90%
Antibacterial agent: 0.5% -2%
Dispersant: 0.5% -2%
Other additives (such as antioxidants, etc.): 0.1% -0.5%
Filler (optional): 5% -15%
Antistatic masterbatch
LLDPE resin: 75% -85%
Antistatic agent: 5% -10%
Dispersant: 0.5% -2%
Other additives (such as antioxidants, etc.): 0.1% -0.5%
Filler (optional): 10% -20%
Color matching LLDPE masterbatch
LLDPE resin: 70% -90%
Pigments or color powders: 1% -10%
Dispersant: 0.5% -2%
Other additives (such as antioxidants, etc.): 0.1% -0.5%
Filler (optional): 5% -20%
These formula ratios are for reference only and need to be adjusted and optimized according to specific production equipment, process conditions, and product quality requirements in actual production.
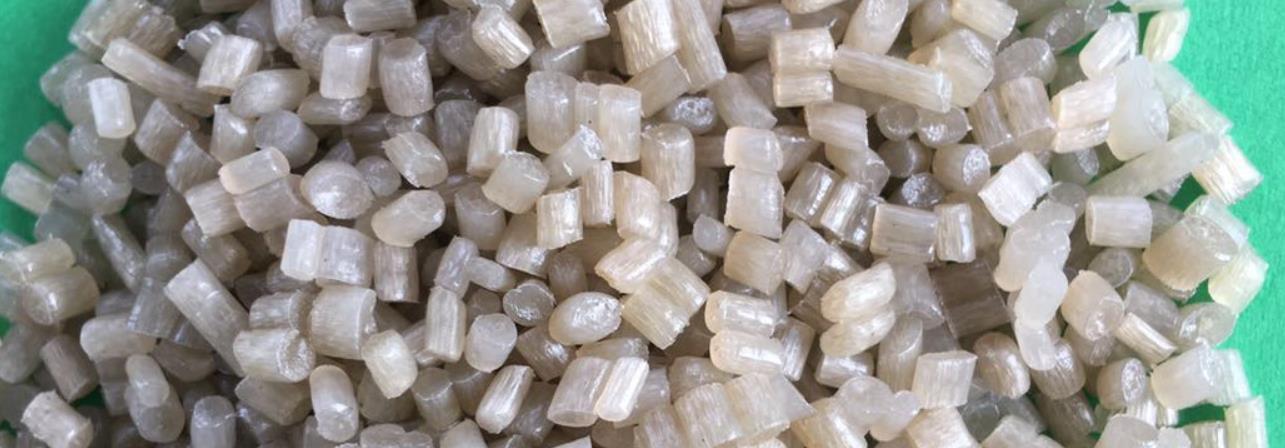
Production process
The production process of LLDPE masterbatch usually includes steps such as raw material preparation, mixing, extrusion, cooling, and cutting, as follows:
1. Raw material preparation
Resin selection: Select the appropriate grade of LLDPE resin based on product performance requirements to ensure good flowability, mechanical properties, etc.
Additive preparation: Accurately weigh various additives for different types of masterbatch, such as lubricants, antioxidants, antibacterial agents, pigments, etc. The quality and amount of additives directly affect the performance and quality of the masterbatch.
2. Mixing
High speed mixing: Add LLDPE resin and additives to the high-speed mixer for thorough mixing. By high-speed stirring, the additive is uniformly dispersed on the surface of the resin particles to form a premix. The mixing time is usually 5-15 minutes, depending on the performance of the mixer and the characteristics of the material.
Static mixing: For some masterbatch with high requirements for mixing uniformity, a static mixer will be used for further mixing after high-speed mixing. The static mixer uses a special internal structure to continuously separate and mix materials during the flow process, improving the mixing effect.
3. Extrusion
Preheating: The mixed material is added to the hopper of the extruder. The extruder barrel is usually divided into multiple heating zones, and the material passes through the preheating zone before entering the screw to reach a certain temperature for subsequent plasticization.
Plasticization extrusion: The material is gradually plasticized by heating and shearing in the barrel under the push of the screw. The rotational speed, temperature, and aspect ratio of the screw have a significant impact on the plasticization quality of the material. Generally speaking, the temperature of the extruder is controlled between 150-250 ℃, and the screw speed is 50-300 revolutions per minute. The plasticized material is extruded through the machine head to form continuous strips or sheets.
4. Cooling
Water cooling: The extruded material is usually cooled by water cooling. Pass the extruded strip or sheet through a sink to rapidly cool the material and solidify it into shape. The water temperature in the sink is generally controlled at 20-40 ℃, and the cooling rate should be moderate. If it is too fast, it may cause stress inside the material, while if it is too slow, it will affect production efficiency.
Air cooling: For some masterbatch with high surface quality requirements, air cooling or a combination of air and cold water cooling can be used. Air cooling uses a fan to blow cold air onto the surface of the material, cooling it down. Air cooling can reduce surface water stains and other issues that may be caused by water cooling, and improve the appearance quality of products.
5. Granulation
Hot cutting: When using the hot cutting method, a cutting device is installed at the head of the extruder to directly cut the extruded material into particles in an incompletely cooled state. The advantages of being eager are high production efficiency and regular particle shape, but the requirements for cutting tools are high and need to be replaced regularly.
Cold cutting: Cold cutting is the process of transporting cooled materials through a traction device to a pelletizer for pelletizing. Cold cut particles have good quality and high dimensional accuracy, but their production efficiency is relatively low. After cutting the particles, they can be screened, packaged, and other processes to obtain the finished LLDPE masterbatch.
In the production process, it is necessary to strictly control the process parameters of each link to ensure the quality stability and performance of the masterbatch meet the requirements. At the same time, regular maintenance and upkeep of production equipment should be carried out to ensure its normal operation.
Production equipment
The equipment for producing LLDPE masterbatch mainly includes raw material processing equipment, mixing equipment, extrusion equipment, cooling equipment, pelletizing equipment, and auxiliary equipment. The following is a specific introduction:
1. Raw material processing equipment
Drying machine: used for drying LLDPE resin and some additives to remove moisture from the raw materials. Common ones include hot air circulation dryers, dehumidification dryers, etc.
Screening machine: Screen the raw materials to remove impurities and particles with particle sizes that do not meet the requirements, ensuring the purity of the raw materials. Vibration screen is a commonly used screening equipment.
2. Hybrid equipment
High speed mixer: Fully mix LLDPE resin with various additives to evenly distribute the additives in the resin. It consists of a stirring blade, a mixing container, a driving device, etc., and has the characteristics of fast mixing speed and good mixing effect.
Static mixer: usually installed before the feed inlet of the extruder, it further mixes the materials that have been mixed at high speed to improve the uniformity of the materials. It has no moving parts and relies on a special internal structure to achieve mixing of materials during the flow process.
3. Extrusion equipment
Single screw extruder: With a simple structure and easy operation, it is suitable for the production of LLDPE masterbatch with general requirements. It consists of screws, barrels, heating and cooling systems, transmission devices, and other components. The material is propelled forward by the rotation of the screw, while the heating of the barrel plasticizes and extrudes the material.
Twin screw extruder: With better mixing, dispersion, and shear performance, it can handle the production of masterbatch with high filling and high-performance requirements. The two screws of the twin-screw extruder mesh with each other, thoroughly stirring and mixing the material during rotation, allowing the additive to better bond with the resin.
4. Cooling equipment
Sink: Used for water-cooled cooling, usually made of stainless steel, with a certain length and width to ensure sufficient cooling time for materials in water. The sink is equipped with a circulating water system to maintain stable water temperature.
Fan: Used for air cooling, blowing cold air towards the extruded material to cool it. According to production needs, different power and types of fans can be selected, such as centrifugal fans, axial fans, etc.
5. Granulation equipment
Hot cutting machine: Installed at the head of the extruder, it cuts the material into pellets before it has completely cooled down. It mainly consists of a cutting blade, a tool holder, a driving device, etc. The speed and position of the cutting blade can be adjusted according to the particle size.
Cold cutting machine: used to cut cooled materials into granules. It usually uses a combination of rotating and fixed cutting tools to cut the material into the desired size. The cold granulator has high particle size accuracy and is suitable for products with high requirements for particle quality.
6. Auxiliary equipment
Traction machine: used to pull the extruded material from the extruder to the cooling equipment and cutting equipment, ensuring continuous transportation of the material. The speed of the tractor can be adjusted according to the extrusion speed to control the length and shape of the particles.
Measuring equipment: including electronic scales, flow meters, etc., used to accurately measure the amount of various raw materials and additives, ensuring the accuracy of formulas and the stability of product quality.
Packaging equipment: Packaging the produced LLDPE masterbatch, commonly using automatic packaging machines that can complete measurement, bagging, sealing, and other processes to improve packaging efficiency and quality.
LLDPE masterbatch extruder
Kerke’s masterbatch extruder can be used to produce LLDPE masterbatch. Our LLDPE masterbatch extruder has multiple models to choose from, which can meet different production requirements.
-
Лабораторный двухшнековый экструдер
When will you need a lab twin screw extruder? If you want to make trials and tests of…
-
Параллельный двухшнековый экструдер
Our Parallel Co-rotating twin screw extruder is designed for compounding and masterbatch making with an output capacity from…
-
Тройной (3 винта) Экструдер
3 Screws extruder is a new technology that has many advantages. The triple screw extruder is mainly used…
-
Двухступенчатая система экструзии
Mother-baby extrusion system is designed for special materials which can not process on one stage extruder, the first…
-
Линия для замешивания компаундов Banbury Kneader
Our kneader + extruder is designed for making special applications with an output capacity from 30kg/h to 1000kg/h.…
-
Система резки / Система гранулирования
Different material needs different cutting system, Kerke provides all kinds of cutting system, here is the explanation of…
Related requirements
When producing LLDPE masterbatch, there are a series of requirements in terms of raw materials, personnel, environment, quality control, etc. The following are specific instructions:
Raw material requirements
LLDPE resin: The appropriate LLDPE resin grade should be selected based on the end use and performance requirements of the product. The melt flow rate, density, molecular weight distribution and other indicators of the resin need to meet the design requirements of specific masterbatch products to ensure that the masterbatch has good processing and application performance.
Additives: The quality of additives is crucial. For example, the lubricant should be able to effectively reduce the friction coefficient of the film surface; Antioxidants need to have good antioxidant properties to extend the service life of masterbatch and products; Pigments should have high coloring power, good dispersibility, and weather resistance. All additives should comply with relevant food hygiene and environmental standards, especially for masterbatch used in food packaging and other fields.
Personnel requirements
Professional knowledge: Production personnel need to have relevant professional knowledge in polymer materials, plastic processing, etc., familiar with the production process and equipment operation principles of LLDPE masterbatch. Understand the performance characteristics of raw materials, the role of additives, and the impact of various parameters on product quality during the production process, in order to accurately judge and solve problems that arise in production.
Operational skills: Proficient in operating production equipment, including starting, debugging, operating, and maintaining extruders, mixers, pelletizers, and other equipment. Being able to accurately set and adjust equipment parameters such as temperature, speed, pressure, etc. according to process requirements, ensuring the stability of the production process and consistency of product quality.
Quality awareness: Possess strong quality awareness, strictly abide by the quality management system and operating procedures, pay attention to details in the production process, and strictly control product quality. Being able to promptly identify product quality issues and take effective measures for improvement and prevention.
Environmental requirements
Temperature and humidity: The temperature and humidity in the production workshop should be maintained within a certain range. Generally speaking, it is more suitable to control the temperature between 20-30 ℃ and the humidity between 40% and 60%. Excessive or insufficient temperature and humidity may affect the performance of raw materials, equipment operation, and product quality. For example, high humidity may cause the raw materials to absorb water, affecting the processing performance and appearance quality of the masterbatch.
Cleanliness and hygiene: The production environment should be kept clean and hygienic to prevent pollutants such as dust and impurities from entering the raw materials and products. The workshop floor should be regularly cleaned and mopped, and the equipment should be regularly cleaned and maintained to prevent impurities such as oil stains and rust from entering the materials. For workshops producing masterbatch for food packaging, hygiene requirements are stricter and must comply with relevant food hygiene standards.
Ventilation and air exchange: The workshop should have good ventilation and air exchange conditions to timely discharge the waste gas and odors generated during the production process. This is not only beneficial for the physical health of operators, but also avoids the adverse effects of exhaust gas on the quality of raw materials and products.
Quality control requirements
Raw material inspection: Each batch of raw materials and additives entering the factory must undergo strict inspection, including testing of appearance, physical properties, chemical properties, and other aspects. For example, detecting the melt flow rate, density, purity of additives, and content of active ingredients of LLDPE resin to ensure that the raw materials meet quality requirements. Only raw materials that pass inspection can be put into production.
Process control: During the production process, it is necessary to strictly control key process parameters such as extrusion temperature, screw speed, mixing time, etc. Regularly maintain and upkeep production equipment to ensure its normal operation and ensure the stability of product quality. At the same time, sampling and testing should be conducted on semi-finished products during the production process, such as checking the uniformity of mixed materials, the appearance and performance of extruded materials, etc., in order to promptly identify problems and make adjustments.
Finished product inspection: Conduct comprehensive quality inspection on the produced LLDPE masterbatch, including testing of appearance, particle size, melt flow rate, additive content, mechanical properties, thermal stability, and other indicators. Only masterbatch that meets all product standards can be packaged and stored as qualified products for sale. For non-conforming products, analysis and handling should be carried out to identify the causes and take measures to improve them, in order to prevent similar problems from happening again.
Приложение
LLDPE masterbatch has a wide range of applications, mainly including the following fields:
1. Plastic film
Agricultural film: LLDPE masterbatch is an important raw material for producing agricultural film. It can improve the tensile strength, puncture resistance, and weather resistance of the film, making it more durable and able to resist the erosion of natural factors such as wind, sun, and rain, extending its service life. At the same time, it can also improve the transparency and insulation performance of the film, providing a good growth environment for crops and promoting their growth and development.
Packaging film: In the packaging field, LLDPE masterbatch is commonly used to produce various packaging films, such as food packaging film, daily necessities packaging film, etc. It can make the film have good flexibility, transparency, and heat sealing properties, which can tightly wrap the product and play a protective and fresh-keeping role. In addition, LLDPE masterbatch can endow the film with certain anti-static properties, reducing the phenomenon of dust and impurities being adsorbed by the film during use.
2. Pipe materials
Water supply pipes: LLDPE masterbatch can be used to manufacture water supply pipes, which have the advantages of corrosion resistance, wear resistance, and high pressure resistance. The pipes produced with it have smooth inner walls, low water flow resistance, and are not easy to scale, which can ensure the efficiency of water transportation and water quality safety. Meanwhile, LLDPE pipes also have good flexibility, making them easy to install and construct, and can be widely used in urban water supply, rural drinking water safety and other projects.
Drainage pipes: LLDPE masterbatch is also widely used in drainage pipes. It can make the pipe have good chemical corrosion resistance and environmental stress cracking resistance, and can withstand the erosion of various sewage and wastewater. In addition, LLDPE drainage pipes are lightweight, easy to handle and install, and can reduce construction costs.
3. Injection molded products
Plastic containers: LLDPE masterbatch can be used to produce various plastic containers, such as plastic buckets, plastic pots, plastic boxes, etc. It can improve the strength and toughness of plastic containers, making them have good impact resistance and durability. Meanwhile, LLDPE masterbatch can also improve the surface glossiness and texture of plastic containers, enhancing the aesthetic appeal of products.
Industrial components: In the industrial field, LLDPE masterbatch can be used to manufacture some wear-resistant and corrosion-resistant industrial components, such as gears, bearings, sliders, etc. It has good self-lubricating properties and low friction coefficient, which can reduce wear and friction between components, improve equipment operating efficiency and service life.
4. Wires and cables
Insulation layer: LLDPE masterbatch has good electrical insulation properties and can be used to produce insulation layers for wires and cables. It can effectively isolate current, prevent leakage and short circuit phenomena, and ensure the safe operation of wires and cables. At the same time, LLDPE insulation layer also has properties such as aging resistance and low temperature resistance, which can adapt to different working environments.
Sheath: LLDPE masterbatch can also be used to manufacture sheaths for wires and cables, which protect the internal structure of wires and cables. It has good mechanical properties and corrosion resistance, which can resist external mechanical damage, chemical corrosion, and moisture intrusion, extending the service life of wires and cables.
5. Other fields
Fiber products: LLDPE masterbatch can be used to produce fiber products such as non-woven fabrics, ropes, fishing nets, etc. It can give fibers good strength and flexibility, improving the quality and performance of fiber products.
Foam products: In the field of foam products, LLDPE masterbatch can be used as one of the main raw materials to produce various foam plastics, such as polystyrene foam board, polyurethane foam, etc. It can improve the performance of foamed plastics, making it have good thermal insulation, heat insulation, sound insulation and cushioning properties.