ETFE masterbatch is a high-performance plastic masterbatch based on ethylene tetrafluoroethylene copolymer (ETFE), belonging to a type of fluorine masterbatch. Fluorine masterbatch is a chain alkane polymer in which some or all hydrogen atoms are replaced by fluorine. ETFE masterbatch is made into granular products using ETFE resin as a carrier, by adding specific proportions of pigments, dispersants, and other additives through mixing, melt extrusion, and other processes. Its core advantage lies in retaining the excellent performance of ETFE resin while achieving color customization and functional modification.
Characteristic
Chemical resistance
Almost insoluble in any organic solvent, resistant to strong acids, alkalis, and corrosive chemicals, suitable for harsh environments such as chemical and semiconductor industries.
Temperature resistance
The long-term use temperature range is -200 ℃ to 150 ℃, and the short-term temperature resistance can reach 200 ℃, meeting the needs of extreme temperature scenarios.
Mechanical properties
High strength, high toughness, strong impact resistance, suitable for manufacturing structural components under complex working conditions.
Transparency and Optical Performance
With a light transmittance of up to 95% and low haze, it is widely used in fields such as optical films and architectural films.
Processability
Excellent fluidity, capable of forming complex shapes through processes such as blow molding, extrusion, injection molding, etc., with minimal performance loss during processing.
Environmental Protection and Safety
Compliant with ROHS standards, free of heavy metals such as cadmium, lead, chromium, etc., it can be used for food contact grade applications (such as medical device components).
Types
Classified by color: including color masterbatch of various colors such as red, yellow, blue, green, white, black, etc., different colors can be provided for ETFE products according to specific needs.
Classified by function:
Ordinary dyeing masterbatch: mainly used to provide basic color for ETFE resin, giving it a certain degree of decoration and identification, meeting the color requirements of different application scenarios.
Functional masterbatch: In addition to staining function, it also has special functions. Like weather resistant masterbatch, it can improve the aging resistance and UV resistance of ETFE products in outdoor environments, extending their service life; Flame retardant masterbatch can make ETFE products flame-retardant, improve their fire safety performance, and is suitable for occasions with high fire protection requirements; Antibacterial masterbatch can endow ETFE products with antibacterial properties and can be used in fields such as healthcare and food packaging; Conductive masterbatch can give ETFE a certain degree of conductivity and can be applied in electronic and electrical applications that require anti-static or conductive properties.
Classified by pigment composition:
Organic pigment masterbatch: Using organic pigments as coloring agents, it has bright colors and good dyeing effects, and can be used for extruding ETFE resins of most colors. Organic pigments can be divided into two types: solvent based and solid based. Solid based organic pigments are prepared by mixing pigment powder and additives through processes such as precision grinding and sieving.
Inorganic pigment masterbatch: made of inorganic pigment powders such as metals, metal oxides, and metal salts, suitable for ETFE resin extrusion in high temperature and high light environments, with good heat and light resistance.
In addition, there are some special types of ETFE masterbatch, such as masterbatch used for specific processing techniques, or masterbatch with specific performance combinations developed for special application fields.
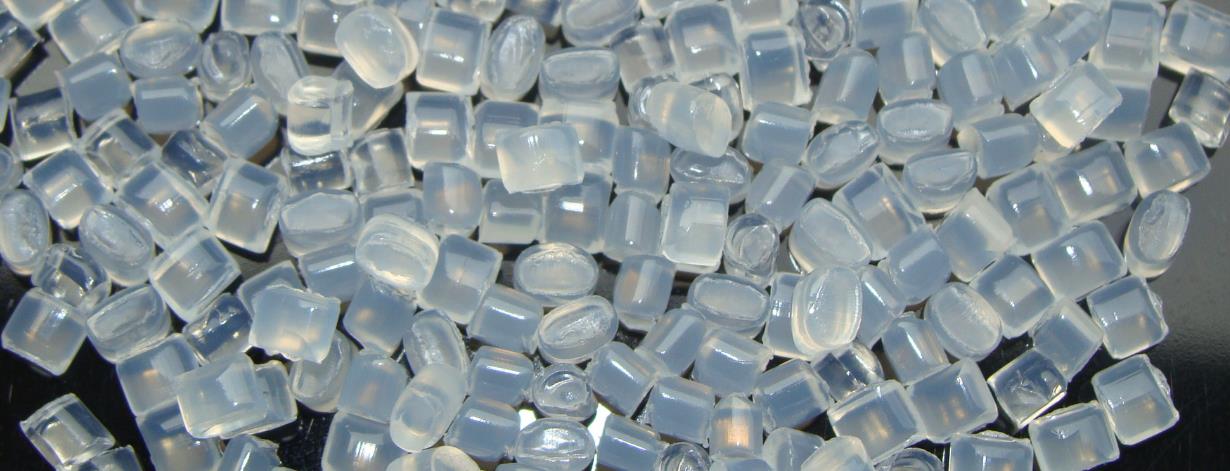
Formula ratio
The formula ratio of ETFE masterbatch may vary depending on different application and performance requirements. The following are some common formula ratio ranges and related explanations:
Proportion of coloring masterbatch formula:
Coloring agents: generally 0.5-2 parts, such as nanoscale pigment powders, including phthalocyanine blue, cobalt blue, phthalocyanine green, cobalt green, iron red, pigment red, pigment yellow, pigment purple, carbon black, and titanium dioxide, with particle sizes typically ranging from 20-500 nm.
Carrier resin: 20-40 parts, usually using the same resin as ETFE as the carrier to ensure compatibility with ETFE.
Dispersant: 0.5-2 parts, can be selected from polytetrafluoroethylene micro powder, ethylene based distearamide, zinc stearate, etc. Among them, the particle size of polytetrafluoroethylene micro powder is below 2 μ m.
Other additives: 1-4 parts of coupling agent, 4-6 parts of plastic plasticizer, 1-5 parts of antistatic agent, 1-5 parts of heat stabilizer, 1-6 parts of ceramic micro powder, 0-6 parts of antifungal agent, 3-7 parts of antioxidant, etc.
Example of formula ratio for other functional masterbatch:
Weathering masterbatch: Typically, ETFE resin accounts for 60-80 parts, antioxidant 2-5 parts, UV absorber 1-3 parts, hindered amine light stabilizer 1-3 parts, and other additives such as dispersants and processing aids 1-5 parts.
Flame retardant masterbatch: 50-70 parts ETFE resin, 20-40 parts flame retardant, 2-5 parts synergist (such as antimony trioxide, etc.), 1-3 parts dispersant, 0.5-2 parts processing aid.
Antibacterial masterbatch: 70-90 parts ETFE resin, 0.5-5 parts antibacterial agent, 1-3 parts dispersant, 0.5-2 parts processing aid. Antibacterial agents can be silver based antibacterial agents, organic antibacterial agents, etc.
Formula ratio of universal ETFE masterbatch:
ETFE resin: 65-85%, is the main component of the masterbatch, providing basic properties.
Dispersant: 3-6%, helps to evenly disperse pigments or additives in the resin.
Processing aids: 0.1-1.5%, improve processing performance, such as increasing fluidity, demolding, etc.
It should be noted that the above formula ratios are for reference only. In actual production, adjustments and optimizations need to be made based on specific product requirements, production processes, and raw material characteristics.
Production process
The production process of ETFE masterbatch generally includes the following main steps:
Raw material preparation
Resin selection: Based on product performance requirements, select appropriate ETFE (ethylene tetrafluoroethylene copolymer) resin particles as the basic raw material to ensure that their purity, molecular weight distribution, and other indicators meet production requirements.
Additive preparation: Accurately weigh various additives according to the formula, such as colorants, dispersants, functional additives, etc. The quality and purity of additives have a significant impact on the performance of masterbatch and need to be strictly controlled.
Mix
High speed mixing: Add the weighed ETFE resin and additives into the high-speed mixer for thorough mixing. By high-speed stirring, the additive is uniformly dispersed on the surface of the resin particles to form a preliminary mixture. The mixing time is usually around 10-30 minutes, depending on the formula and equipment performance.
Squeeze out
Melt extrusion: Put the mixed material into a twin-screw extruder. The barrel of the extruder heats the material to a certain temperature through a heating device, causing the ETFE resin to melt, and at the same time, the additives are evenly integrated into the resin melt. The extrusion temperature is generally controlled between 250-300 ℃, and the specific temperature needs to be adjusted according to the type of ETFE resin and the characteristics of the additives.
Screw extrusion: Under the rotation of the screw, the material undergoes processes such as conveying, compression, melting, mixing, and extrusion inside the extruder. The parameters such as screw speed and aspect ratio have a significant impact on the mixing effect and extrusion quality of materials, and the screw speed is usually between 100-500 revolutions per minute.
Granulation
Underwater pelletizing: The molten material extruded from the extruder forms a continuous strip through the die, and then enters the underwater pelletizing system. In the underwater granulator, the high-speed rotating cutter cuts the strip into uniform particles, and the size and shape of the particles can be controlled by adjusting the speed of the cutter and the aperture of the die.
Air cooled granulation: For some ETFE masterbatch with special requirements, air cooled granulation can also be used. The extruded strip is cooled and solidified by an air cooling device, and then enters the granulator to be cut into particles. The surface of particles produced by air-cooled granulation is relatively smooth, but the production efficiency is relatively low.
Screening and packaging
Screening: The granulated ETFE masterbatch is screened through a vibrating screen to remove particles that are too large or too small, ensuring the uniformity of the product’s particle size. Generally, the appropriate mesh size is selected for screening according to the specifications of the product.
Packaging: The qualified masterbatch after screening is sealed and usually packaged in plastic woven bags or aluminum foil bags to prevent moisture, oxidation, and other factors that may affect product quality. The packaged masterbatch is stored in a dry and ventilated warehouse, waiting for factory sales.
Throughout the entire production process, it is necessary to strictly control the process parameters of each link and regularly maintain and upkeep the equipment to ensure the stability and consistency of product quality. At the same time, it is necessary to conduct quality testing on the ETFE masterbatch produced, including inspection of appearance, particle size distribution, flowability, coloring power, functional characteristics, etc. Only products that pass the testing can enter the market.
Production equipment
The ETFE masterbatch production equipment mainly includes the following types:
Mixing equipment
High speed mixer: used to thoroughly mix ETFE resin with various additives. It achieves uniform mixing of materials in a short period of time through high-speed rotating stirring blades. It has the advantages of high mixing efficiency and good mixing uniformity, which can ensure the uniform dispersion of additives in the resin and lay the foundation for subsequent production.
Extrusion equipment
Twin screw extruder: It is one of the core equipment for ETFE masterbatch production. The two interlocking screws rotate inside the barrel, pushing the material forward. During this process, the material undergoes stages such as heating, melting, and mixing. Twin screw extruders have good mixing performance, conveying capacity, and self-cleaning ability, which can accurately control the residence time and extrusion temperature of materials, ensuring the stability of product quality.
Granulation equipment
Underwater pelletizer: usually used in conjunction with twin-screw extruders. The molten material extruded from the extruder die directly enters the water tank of the underwater pelletizer, and under the action of the high-speed rotating cutter, the material is cut into particles. Particles quickly cool and solidify in water, with advantages such as uniform particle size, smooth surface, and high production efficiency. It is a commonly used granulation equipment in ETFE masterbatch production.
Air cooled granulation unit: including air cooling device and granulator. The extruded strip is first cooled and solidified by an air cooling device, and then enters the granulator to be cut into particles. The air-cooled granulation unit is suitable for the production of ETFE masterbatch with special requirements for particle appearance and performance, but its production efficiency is relatively low compared to underwater pelletizers.
Auxiliary equipment
Feeding machine: used to automatically transport ETFE resin and additives into the hopper of the mixer or extruder, achieving automatic feeding of materials, improving production efficiency, and reducing manual labor intensity. Common feeding machines include screw feeding machines, vacuum feeding machines, etc.
Drying machine: Before production, dry ETFE resin and some hygroscopic additives to remove moisture from the material and prevent quality problems such as bubbles and surface defects caused by moisture during extrusion. Common drying equipment includes hot air circulation dryer, dehumidification dryer, etc.
Cooling equipment: In addition to the water tank in the underwater pelletizer as a cooling device, other cooling equipment may also be required throughout the production process, such as a cooling circulating water system, to cool the extruder barrel, molds, and other components, ensuring that the equipment operates within the normal temperature range and guaranteeing product quality and equipment service life.
Screening equipment: The ETFE masterbatch after granulation is screened using a vibrating screen to remove particles that are too large or too small, ensuring the uniformity of the product’s particle size. According to the specifications of the product, different mesh sizes can be selected for screening.
Test equipment
Particle size analyzer: used to measure the particle size and distribution of ETFE masterbatch, accurately obtaining particle size data through principles such as laser scattering and image analysis, and helping production personnel control the particle size indicators of products.
Melt flow rate meter: measures the melt flow rate of ETFE masterbatch at a certain temperature and pressure, in order to evaluate the processing flowability of masterbatch and ensure the stability of product performance in subsequent processing.
Color difference meter: For colored ETFE masterbatch, the color difference meter is used to measure and analyze the color parameters of the masterbatch, compare them with standard color samples, and control the color consistency and accuracy of the product.
Mechanical performance testing equipment: such as tensile testing machines, impact testing machines, etc., used to test the mechanical properties of samples made of ETFE masterbatch, such as tensile strength, elongation at break, impact strength, etc., to evaluate whether the quality and performance of the product meet the requirements.
ETFE masterbatch extruder
Kerke’s masterbatch extruder can be used to produce ETFE masterbatch. Our ETFE masterbatch extruder has multiple models to choose from, which can meet different production requirements.
-
Лабораторный двухшнековый экструдер
When will you need a lab twin screw extruder? If you want to make trials and tests of…
-
Параллельный двухшнековый экструдер
Our Parallel Co-rotating twin screw extruder is designed for compounding and masterbatch making with an output capacity from…
-
Тройной (3 винта) Экструдер
3 Screws extruder is a new technology that has many advantages. The triple screw extruder is mainly used…
-
Двухступенчатая система экструзии
Mother-baby extrusion system is designed for special materials which can not process on one stage extruder, the first…
-
Линия для замешивания компаундов Banbury Kneader
Our kneader + extruder is designed for making special applications with an output capacity from 30kg/h to 1000kg/h.…
-
Система резки / Система гранулирования
Different material needs different cutting system, Kerke provides all kinds of cutting system, here is the explanation of…
Related requirements
In the production of ETFE masterbatch, the extruder needs to meet the following requirements:
Good plasticizing ability
ETFE resin has a high melting point and a certain viscosity, so the extruder needs to have sufficient heating power and shear capacity to achieve full plasticization of ETFE resin. It is usually required that the material barrel of the extruder can be quickly heated to 250-300 ℃ and maintained at a stable temperature. At the same time, the design of the screw should be able to generate appropriate shear force, so that the resin can be mixed evenly during the melting process, avoiding local unmelted or poorly plasticized situations.
Accurate temperature control
The production of ETFE masterbatch has strict temperature requirements. Excessive temperature may lead to resin decomposition, additive failure, and affect the performance of masterbatch; If the temperature is too low, it will cause incomplete plasticization of the resin and make extrusion difficult. The extruder needs to be equipped with a high-precision temperature control system, such as thermocouples, temperature control instruments, etc., which can accurately control the temperature of each section of the material barrel, with an error range controlled within ± 2 ℃, to ensure that the material is extruded in a stable temperature environment and ensure the stability of product quality.
Stable material transportation
In order to ensure the quality uniformity of ETFE masterbatch, the extruder needs to provide stable material conveying. The design of the screw should be able to achieve uniform material pushing and avoid material stagnation or backflow in the material barrel. At the same time, the drive system of the extruder should have good stability and speed regulation performance, and be able to accurately adjust the screw speed according to production needs to ensure that the material is extruded at a constant speed. The fluctuation range of the screw speed is usually required to not exceed ± 1%.
Efficient mixing performance
In the production of ETFE masterbatch, it is necessary to thoroughly mix the resin with various additives. The screw structure of the extruder should be conducive to efficient mixing of materials, such as using screws with mixing elements, such as pin screws, barrier screws, etc., which can increase radial mixing and axial conveying of materials, and evenly disperse additives in the resin. In addition, the mixing effect can be improved by optimizing the aspect ratio of the screw. Generally, the aspect ratio of the extruder used for ETFE masterbatch production is more suitable between 30-40.
Corrosion Resistance
Due to the potential corrosiveness of ETFE resin and some additives, especially in high-temperature extrusion environments, they can cause corrosion to components such as the extruder barrel and screw. Therefore, the key components of the extruder need to be made of corrosion-resistant materials, such as chrome plated alloy steel, nickel based alloys, etc., to improve the service life of the equipment, reduce equipment maintenance costs, and ensure production continuity.
Automated Control and Monitoring
Modern ETFE masterbatch production requires extruders to have automated control and monitoring functions. By equipping advanced control systems such as programmable logic controllers (PLCs), real-time monitoring and automatic adjustment of parameters such as temperature, speed, and pressure of the extruder can be achieved. At the same time, it can also be linked and controlled with other production equipment to improve the automation level and production efficiency of the production process, and reduce the impact of human factors on product quality.
Приложение
ETFE masterbatch has various excellent properties, such as chemical corrosion resistance, weather resistance, high transparency, electrical insulation, etc. Therefore, it has a wide range of applications in multiple fields. The following are some of the main application areas:
Wire and cable
Insulation layer: ETFE masterbatch can be used to produce insulation layers for wires and cables. Due to its excellent electrical insulation performance, chemical corrosion resistance, and high temperature resistance, it can effectively protect the conductors inside wires and cables, prevent leakage and short circuits, and extend the service life of wires and cables. Commonly used for wires and cables in special environments such as chemical enterprises and high-temperature workshops.
Sheath: The sheath made of ETFE masterbatch has excellent wear resistance, weather resistance, and chemical corrosion resistance, which can protect wires and cables from external environmental erosion and mechanical damage. ETFE sheathing is often used to improve the reliability and stability of wires and cables used outdoors, such as power transmission lines and wind power cables.
Film
Architectural membrane material: ETFE film has high transparency, self-cleaning, and good weather resistance. Thin films made from ETFE masterbatch are often used in the construction field, such as roofs and walls of large public buildings such as sports venues, exhibition halls, and airport terminals. It can not only provide good lighting effect, but also effectively block the influence of ultraviolet rays and harsh external environment, while reducing the weight of the building structure.
Agricultural film: In the field of agriculture, ETFE film can be used to make greenhouse film. It has good transparency and thermal insulation properties, which can provide sufficient light and suitable growth environment for crops. At the same time, it also has a certain degree of chemical corrosion resistance, which can resist the erosion of pesticides and fertilizers, and extend the service life of the film.
Injection molding products
Chemical containers: By utilizing the chemical corrosion resistance and high temperature resistance of ETFE masterbatch, various chemical containers such as reaction vessels, storage tanks, pipelines, etc. can be injection molded. These chemical containers can withstand the corrosion of various chemical substances, ensuring the safety and stability of the chemical production process.
Electronic and electrical components: Injection molded products made from ETFE masterbatch can also be applied in the field of electronic and electrical components, such as electronic component casings, insulation brackets, etc. Its excellent electrical insulation performance and temperature resistance can ensure the normal operation and safety of electronic and electrical equipment.
Fibre
Industrial filtration materials: ETFE fibers have chemical corrosion resistance, high temperature resistance, and good filtration performance, and can be used to make industrial filtration materials, such as acid and alkali filtration in the chemical industry, metal liquid filtration in the metallurgical industry, etc. It can effectively filter impurities, improve product quality, and extend the service life of filter materials.
Special clothing: In some special industries such as firefighting, chemical engineering, electricity, etc., it is necessary to wear clothing with protective properties. ETFE fiber can be used to make these special garments, which have properties such as fire resistance, chemical corrosion resistance, and anti-static, providing effective protection for workers.