HIPS masterbatch (impact resistant polystyrene masterbatch) is a widely used additive in plastic processing. It is based on HIPS (impact resistant polystyrene) resin and contains various additives, fillers, or pigments to meet specific processing and performance requirements. HIPS masterbatch is widely used in the production of various plastic products, such as home appliance casings, toys, packaging materials, building materials, etc.
Classification
HIPS masterbatch can be classified based on the functional components added, and common classifications of HIPS masterbatch include:
HIPS flame retardant masterbatch:
Added flame retardant to improve the flame retardancy of HIPS products.
Suitable for disposable items, instruments and meters, household appliances, toys and entertainment products, as well as the construction industry and other fields.
For example, models such as HIPS400, HIPS402, HIPS403, etc.
HIPS antibacterial masterbatch:
Added antibacterial agents to inhibit the growth of bacteria and other microorganisms.
Active zinc oxide HIPS antibacterial masterbatch (such as GINTER HILL) ® HIPS20A03 has the advantages of low dosage, good antibacterial and anti mold effects, and minimal impact on the physical properties of the product.
HIPS color masterbatch:
Added pigments for coloring HIPS products.
Multiple color options are available to meet different appearance needs.
For example, high fluidity wood plastic patterned granite effect marble masterbatch, etc.
HIPS filling masterbatch:
Fillers such as calcium carbonate and talc powder have been added to reduce costs or improve certain properties of the product.
Filling masterbatch can reduce raw material costs while ensuring product performance.
HIPS other functional masterbatch:
According to specific needs, anti-static agents, antioxidants and other additives can be added to make HIPS masterbatch with specific functions.
For example, anti-static masterbatch, antioxidant masterbatch, etc.
These HIPS masterbatch play an important role in plastic processing, and by adding different functional components, they can meet the needs of different fields and application scenarios.
Formula ratio
The formula ratio of HIPS masterbatch varies depending on its specific functions and uses. Here are some examples of formula ratios for common HIPS masterbatch:
1. High flow, high toughness flame retardant HIPS masterbatch
HIPS resin: 4-9%
Toughening agent: 6-12%
Compound flame retardant: 72-83%
Antioxidant: 0.1~1%
Lubricant: 0.1~3%
Processing modified oil: 4-8%
2. Decabromodiphenyl flame retardant HIPS pellets
HIPS:83%
Decabromobiphenyl: 12%
Other additives: appropriate amount (such as Sb ₂ O ∝, etc.)
3. Decabromodiphenyl ether flame retardant HIPS pellets
HIPS:100%
Decabromodiphenyl ether: 13%
Zinc stearate: 1%
Other additives: appropriate amount
4. Tetrabromobisphenol A flame retardant HIPS pellets
HIPS:79%
Tetrabromobisphenol A: 17%
Sb₂O₃:4%
5. HIPS/Bromine/Antimony/Organic Montmorillonite Composite Flame Retardant Granules
HIPS:100%
Tetrabromobisphenol A: 7.5%
Antimony trioxide: 2%
Organic montmorillonite: 5%
6. Low odor flame-retardant and antibacterial HIPS material for electrical appliances
HIPS resin: 4170 parts
Composite flame retardant (bromine based flame retardant: antimony trioxide: phosphate ester flame retardant=1118:36:410): 1832 parts
Antibacterial masterbatch: 1020 parts
Other additives: 2.77 parts
7. Low temperature ultra tough HIPS pellets
HIPS(466F):100%
SBS(YH-792):40%
Calcium carbonate (1-10 μ m): 5%
Antioxidant: 0.5%
EBS:0.5%
8. Talc powder filled HIPS pellets
HIPS:83%
SBS:10%
Talc powder (325 mesh): 5%
Titanium ester coupling agent: 2%
9. HIPS/Titanium Dioxide Nanoparticles
Waste HIPS: 98~99%
TiO₂(20nm):1~2%
Formula ratio analysis
Flame retardant masterbatch: Flame retardant is the core component, and its addition amount is usually high to ensure the flame retardant performance of the product.
Antibacterial masterbatch: The amount of antibacterial agent added should be determined according to specific antibacterial requirements, while considering its impact on product performance.
Filling masterbatch: The amount of filler (such as calcium carbonate, talc powder, etc.) added can be adjusted according to cost requirements and product performance.
Other functional masterbatch: The amount of additives such as toughening agents, antioxidants, lubricants, etc. should be optimized according to specific functional requirements.
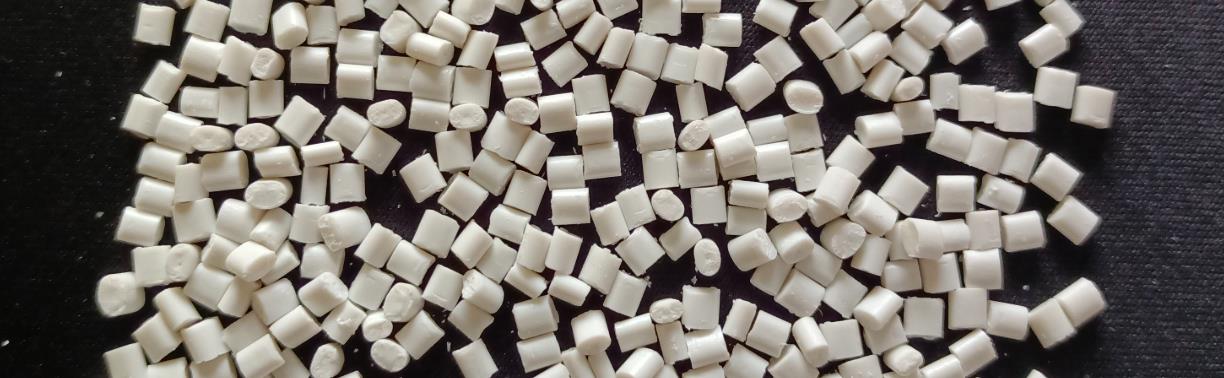
Production process
The production process of HIPS masterbatch usually involves multiple steps to ensure that the quality and performance of the masterbatch meet specific requirements. The following is a general production process for HIPS masterbatch:
1. Raw material preparation
HIPS resin: As the main carrier of masterbatch, it provides basic physical and chemical properties.
Additives: such as flame retardants, antibacterial agents, antioxidants, toughening agents, etc., added according to the specific functional requirements of the masterbatch.
Fillers: such as calcium carbonate, talc powder, etc., used to reduce costs or improve certain properties.
Pigments: Used to color masterbatch to meet specific appearance requirements.
2. Mixing and preprocessing
Mixing: Mix HIPS resin, additives, fillers, pigments and other raw materials evenly in a high-speed mixer according to the formula ratio.
Drying: For some highly hygroscopic raw materials, such as HIPS resin, it may be necessary to dry them before mixing to remove moisture and avoid the formation of bubbles or affecting product quality during processing.
3. Extrusion granulation
Melting: Add the mixed raw materials into a twin-screw extruder and melt them through heating and the shearing action of the screw.
Extrusion: Molten raw materials are extruded through the die of an extruder to form continuous strip-shaped materials.
Granulation: After cooling, the strip-shaped material is cut into uniform granular masterbatch by a granulator.
4. Post processing
Drying: The diced masterbatch may need to be dried to remove surface moisture and prevent clumping or spoilage during storage and use.
Screening: Remove unqualified masterbatch particles, such as oversized or undersized particles, through screening equipment to ensure uniform particle size of the masterbatch particles.
Packaging: Packaging qualified masterbatch for storage and transportation.
5. Quality control
Throughout the entire production process, strict quality control is required for raw materials, intermediate products, and final products to ensure that the quality of the masterbatch meets the standards. This includes testing the purity, content, and physical properties of the raw materials, monitoring parameters such as temperature, pressure, and flow rate during the extrusion process, and testing the particle size, color, melt index, and specific functional properties (such as flame retardancy, antibacterial properties, etc.) of the final masterbatch.
6. Special craftsmanship
For certain HIPS masterbatch with special functions, such as flame retardant masterbatch or antibacterial masterbatch, special processes or additives may need to be used in the production process. For example, flame retardant masterbatch may require the addition of flame retardants and synergists, and special mixing and extrusion processes to ensure uniform distribution of flame retardants in the masterbatch; Antibacterial masterbatch requires the addition of antibacterial agents and appropriate processing techniques to maintain their activity within the masterbatch.
Production equipment
The details of the extruder equipment and related parameters for producing HIPS masterbatch are as follows:
1. Production equipment
двухшнековый экструдер
Type: Twin screw extruder is often used to produce HIPS masterbatch due to its powerful mixing and plasticizing capabilities.
Structure: usually includes feeding port, screw, barrel, heating system, cooling system, cutting system, and other parts.
вспомогательное оборудование
Feeding machine: used to evenly feed raw materials into the extruder.
Drying machine: For some materials with strong moisture absorption, such as HIPS resin, drying treatment may be required before mixing.
Vibration screen: used for screening and removing unqualified masterbatch.
Conveyor belt: used to transport the mother granules after cutting to the next process.
2. Details of relevant parameters
Screw parameters
Screw diameter: determined according to production scale and output requirements, usually ranging from 20mm to 120mm.
Length to diameter ratio (L/D): The length to diameter ratio of twin-screw extruders is usually above 24, with a maximum of 43, to ensure sufficient plasticization time and mixing effect.
Compression ratio: The exhaust screw has its own compression sections in the first and second stages, corresponding to their respective compression ratios, which are usually adjusted according to the physical state of the material.
Temperature parameters
Barrel temperature: The barrel should be divided into multiple heating sections, and the temperature range should be adjusted according to the melting temperature of HIPS resin, usually between 190 ℃ and 220 ℃.
Head temperature: The head temperature is usually slightly lower than the barrel temperature to ensure stable extrusion of the melt.
Particle cutting system parameters
Cutting speed: The cutting speed should be adjusted according to the particle size and yield requirements of the mother particles, usually around 1137v/min.
Disc cutter speed: The disc cutter speed also needs to be adjusted according to specific production needs to ensure uniform cutting effect.
Другие
Motor power: determined according to the specifications and production requirements of the extruder, usually between 4kW and 15kW.
Production capacity: Production capacity is determined based on factors such as the specifications of the extruder and screw speed, typically ranging from tens to hundreds of kilograms per hour.
3. Precautions
Raw material selection: HIPS resin and other raw materials with stable quality and high purity should be selected to ensure the quality of the masterbatch.
Temperature control: The temperature of the material barrel and machine head should be precisely controlled to avoid poor plasticization or degradation caused by excessive or insufficient temperature.
Screw maintenance: The screw should be cleaned and maintained regularly to ensure its good mixing and plasticizing ability.
Safety production: Strict adherence to safety operating procedures should be followed during the production process to ensure the safety of personnel and equipment.
HIPS masterbatch extruder
Kerke’s masterbatch extruder can be used to produce HIPS masterbatch. Our HIPS masterbatch extruder has multiple models to choose from, which can meet different production requirements.
-
Лабораторный двухшнековый экструдер
When will you need a lab twin screw extruder? If you want to make trials and tests of…
-
Параллельный двухшнековый экструдер
Our Parallel Co-rotating twin screw extruder is designed for compounding and masterbatch making with an output capacity from…
-
Тройной (3 винта) Экструдер
3 Screws extruder is a new technology that has many advantages. The triple screw extruder is mainly used…
-
Двухступенчатая система экструзии
Mother-baby extrusion system is designed for special materials which can not process on one stage extruder, the first…
-
Линия для замешивания компаундов Banbury Kneader
Our kneader + extruder is designed for making special applications with an output capacity from 30kg/h to 1000kg/h.…
-
Система резки / Система гранулирования
Different material needs different cutting system, Kerke provides all kinds of cutting system, here is the explanation of…
Related requirements
The requirements for the extruder for producing HIPS masterbatch are as follows:
Screw design:
Screw material: Wear resistant and corrosion-resistant materials such as 38CrMoAlA should be selected to ensure the stability and reliability of the screw during long-term use.
Screw structure: The screw should be designed based on the principle of building blocks, in order to reasonably configure the aspect ratio, pitch, screw components, etc. according to the processing material system and process requirements. For the production of HIPS masterbatch, the screw needs to have good mixing and plasticizing ability to ensure that various raw materials are fully and evenly mixed.
Temperature control:
Accurate temperature control: The extruder should be equipped with a precise temperature control system that can accurately control the temperature of the barrel and head. The temperature of the barrel is usually adjusted according to the melting temperature of HIPS resin, usually between 180~220 ℃. The head temperature is slightly lower than the barrel temperature to ensure stable extrusion of the melt.
Segmented heating: The material barrel should be divided into multiple heating sections for segmented heating according to the plasticization requirements of the material, ensuring uniform and stable temperature during the extrusion process.
Extrusion volume and screw speed:
Extrusion capacity: The extrusion capacity of the extruder should be adjusted according to production needs to meet the production requirements of different scales.
Screw speed: Screw speed is a key factor affecting the production capacity of extruders. For the production of HIPS masterbatch, the screw speed should be reasonably set according to the plasticizing effect of the material and the production capacity requirements of the extruder.
Exhaust system:
Effective exhaust: Due to the possibility of gas generation during the plasticization process of HIPS resin, the extruder should be equipped with an effective exhaust system to eliminate gas, avoid the generation of bubbles, and ensure the quality of the masterbatch.
Granulation system:
Uniform granulation: The granulation system of the extruder should be able to produce uniform granular masterbatch to ensure uniform particle size distribution and facilitate subsequent processing and use.
Adjustable cutting speed: The cutting speed of the cutting system should be adjustable to meet different production needs and ensure the yield and quality of the masterbatch.
Equipment stability and reliability:
High stability: The extruder should have good stability to ensure the continuity and stability of the production process, reduce failures and downtime.
High reliability: The components of the extruder should be made of high-quality materials to ensure the reliability and durability of the equipment.
Convenience of operation and maintenance:
Easy to operate: The operating system of the extruder should be designed to be concise and clear, making it easy for operators to quickly get started and operate proficiently.
Easy maintenance: The various components of the extruder should be easy to disassemble and install, facilitating daily maintenance and upkeep, reducing maintenance costs and time.
Приложение
HIPS masterbatch (impact resistant polystyrene masterbatch) has a wide range of applications in the production of plastic products, which can significantly improve the performance of products and meet the needs of different fields. The following are the main applications of HIPS masterbatch:
1. In the field of household appliances
Application example:
Shell manufacturing: HIPS masterbatch is commonly used to produce shells for household appliances such as refrigerators, air conditioners, and washing machines.
Performance improvement: By adding flame retardant masterbatch, the flame retardant performance of the product can be improved to meet the safety standards of household appliances.
Advantages:
Good appearance: HIPS products have a smooth surface and are easy to color, meeting the high appearance requirements of household appliances.
Cost effectiveness: Compared to other engineering plastics, HIPS materials have lower costs and help reduce the production cost of household appliances.
2. Toys and entertainment products
Application example:
Toy manufacturing: HIPS masterbatch is used to produce various plastic toys, such as building blocks, models, dolls, etc.
Safety performance: Adding antibacterial masterbatch can inhibit bacterial growth and improve the hygiene and safety of toys.
Advantages:
Excellent processing performance: HIPS material is easy to injection mold and can be used to manufacture toys with complex shapes.
Impact resistance: HIPS has high impact resistance, reducing the risk of toys breaking during use.
3. Packaging materials
Application example:
Food packaging: HIPS masterbatch can be used to produce packaging materials such as food containers and trays.
Functional packaging: Adding anti-static masterbatch can prevent packaging materials from generating static electricity during transportation and protect sensitive items such as electronic products.
Advantages:
Health and safety: HIPS materials comply with the safety standards for food contact materials, ensuring food safety.
Moisture resistance: HIPS products have a certain degree of moisture resistance, protecting the contents of the packaging from moisture.
4. Building and decorative materials
Application example:
Indoor decoration: HIPS masterbatch is used for producing decorative lines, wall panels, ceilings, etc.
Outdoor application: Adding UV absorbers can improve the weather resistance of HIPS products and is suitable for outdoor decoration.
Advantages:
Beautiful and durable: HIPS products can undergo various surface treatments, such as embossing and film coating, to meet different decorative needs.
Easy installation: HIPS material is lightweight and high-strength, easy to handle and install, reducing construction costs.
5. Automotive components
Application example:
Interior parts: HIPS masterbatch is used to produce interior components such as car dashboards, door panels, seats, etc.
Functional components: Adding flame retardant and reinforcing masterbatch can improve the heat resistance and mechanical strength of the product.
Advantages:
Lightweight design: HIPS material has low density, which helps reduce the weight of the car and improve fuel economy.
Cost effectiveness: Compared to metals and advanced engineering plastics, HIPS materials have lower costs and lower automotive manufacturing costs.
6. Daily necessities and consumer goods
Application example:
Home goods: HIPS masterbatch is used for producing storage boxes, hangers, bathroom products, etc.
Office supplies: production folders, pen holders, display racks, etc.
Advantages:
Flexible design: HIPS material is easy to color and shape, allowing for the production of products with rich colors and diverse shapes.
Durability: HIPS products have good chemical corrosion resistance, extending the product’s service life.
7. Electronic and electrical field
Application example:
Shell and components: HIPS masterbatch is used to produce the shell and internal components of electronic products such as televisions, computers, printers, etc.
Electromagnetic shielding: Adding conductive masterbatch can endow HIPS products with electromagnetic shielding function, protecting electronic components from interference.
Advantages:
Insulation performance: HIPS material has good electrical insulation properties, ensuring the safe use of electronic products.
High processing efficiency: HIPS materials are easy to process, improving production efficiency and reducing manufacturing costs.
8. Medical and hygiene products
Application example:
Medical devices: HIPS masterbatch is used to produce some non critical medical device casings and components.
Sanitary products: production of medical waste containers, disposable items, etc.
Advantages:
Health and safety: HIPS materials can improve the antibacterial performance of products by adding antibacterial agents, meeting the requirements of medical environments.
Cost controllable: HIPS material has a lower cost and is suitable for the production of disposable medical supplies.
Summary:
HIPS masterbatch has been widely used in multiple fields due to its excellent processing performance, good physical and mechanical properties, and cost-effectiveness. By adding different functional additives such as flame retardants, antibacterial agents, anti-static agents, etc., HIPS masterbatch can endow products with specific properties to meet the needs of different industries. With the continuous progress of materials science, the application scope of HIPS masterbatch will be further expanded, providing more high-performance and multifunctional plastic solutions for various industries.