Wood pellet is a biomass formed fuel made from wood fiber materials (such as bark, sawdust, forestry residues, or crop straw) through processing. It belongs to a type of biomass fuel, which compresses wood raw materials into cylindrical particles with a diameter of 6-8 millimeters and a length 4-5 times the diameter, making it easy to store and transport. Wood chips, as a clean and efficient biomass fuel, play an important role in the global energy transition. Its renewability, environmental friendliness, and economic viability make it an ideal alternative to fossil fuels, widely used in fields such as energy, environmental protection, and agriculture. With technological progress and policy support, the market prospects for wood pellets are broad, and they are expected to become a key force in promoting low-carbon economic development.
Characteristic
Combustibility
Efficient combustion: The combustion efficiency exceeds 80% (about 60% for ordinary coal), with a calorific value of 3900-4800 kcal/kg, and can reach 7000-8000 kcal/kg after carbonization.
Clean and environmentally friendly: Low sulfur and phosphorus content, low emissions of sulfur dioxide and phosphorus pentoxide during combustion, and high-quality organic potassium fertilizer in ash that can be recycled.
Physical property
High density: The density is 0.9-1.4g/cm ³, with a small volume (only 1/15 of the same weight of sawdust), making it easy to store and transport.
Uniformity: Consistent particle size, stable combustion, and easy implementation of automated feeding.
Types
Wood chips can be classified into various types according to different classification criteria. The following are common classification methods and corresponding types:
Classified by raw materials
Pure sawdust pellets: These pellets are made entirely from sawdust and do not contain any other impurities. It has high combustion efficiency, produces less ash, and releases relatively less pollutants during the combustion process, making it a high-quality biomass fuel. For example, pure wood chips made from single types of wood such as pine and birch have high heat generation and stable combustion performance.
Mixed wood chips: usually made by mixing multiple types of wood chips, and may also contain small amounts of other biomass materials such as sawdust, tree branches, etc. This type of particle has a wide range of raw material sources and relatively low cost, but its combustion characteristics may vary depending on the different raw materials. For example, the combustion performance of particles made by mixing wood chips of hardwood and cork is between that of pure hardwood particles and pure cork particles.
Classify by shape
Cylindrical sawdust particles: This is the most common shape, typically with a diameter between 6-10 millimeters and a length of 20-30 millimeters. The production process of cylindrical particles is relatively simple, easy to shape, and convenient for storage and transportation. At the same time, they can burn evenly in combustion equipment and provide stable heat.
Flake wood chips: They are thin flakes, usually with a thickness of about 1-3 millimeters. The surface area of sheet-like particles is relatively large, and the contact area with air during combustion is large, resulting in a fast combustion rate and the ability to quickly release heat. However, due to its unique shape, special packaging and handling may be required during storage and transportation to prevent breakage and scattering.
Function
Wood chips for heating: mainly used for heating in homes, offices, schools, and other places. These types of particles require high combustion efficiency, stable heat generation, and minimal pollutants generated during the combustion process to ensure indoor air quality. Usually, there are high requirements for the density, calorific value, and other indicators of particles. The density is generally between 600-1000 kg/cubic meter, and the calorific value is around 4000-5000 kcal/kg.
Industrial sawdust pellets: used for combustion heating or power generation in industrial fields such as boilers and power plants. Industrial pellets have high requirements for yield and combustion stability, and are usually produced using large-scale production equipment. The quality standards may vary depending on different industrial applications, but generally require a higher density of particles to improve combustion efficiency and facilitate storage and transportation. For example, the density of some industrial wood chips can reach 1100-1300 kilograms per cubic meter.
Barbecue wood chips: specifically used for processing grilled and smoked foods. This type of particle is usually made from wood with a special aroma, such as apple wood, cherry wood, walnut wood, etc., which can release a unique aroma when burned, adding flavor to food. The size of wood chips used for barbecue is generally small and the shape is relatively regular, which facilitates uniform combustion and smoke control in barbecue equipment.
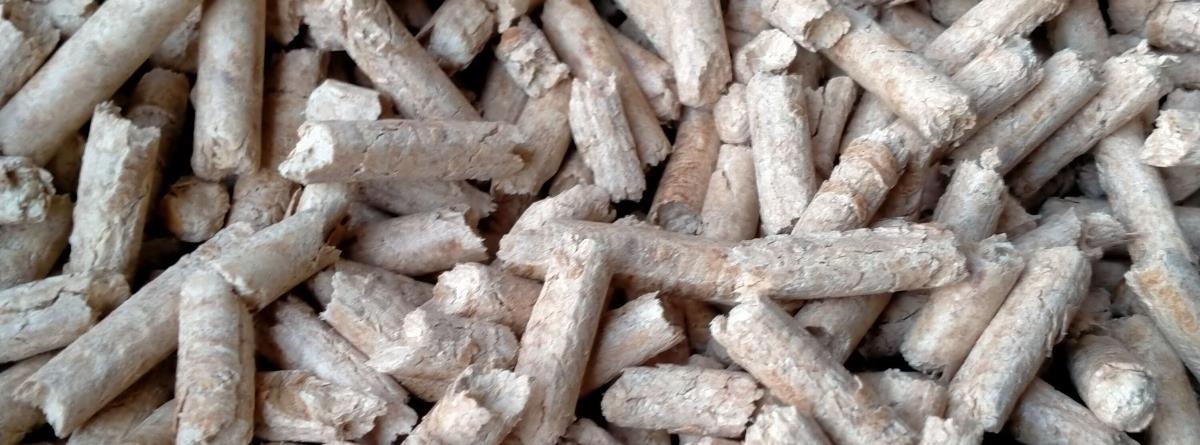
Formula ratio
The formula ratio of wood chips may vary depending on the type of raw materials, usage, and production process. Here are some common formula ratio examples:
Pure wood pellets
Usually only a single type of sawdust is used, such as pine sawdust, poplar sawdust, etc., and the particle size of sawdust is generally required to be around 2-5 millimeters. Taking pine sawdust as an example, the formula ratio is 100% pine sawdust. Due to the presence of certain oils and fats in pine wood, it can provide a higher calorific value during combustion, but may produce more smoke.
Mixed wood pellets
Hardwood and Cork Mixed: Hardwood chips (such as birch, oak, etc.) account for 60% -80%, while soft wood chips (such as pine, spruce, etc.) account for 20% -40%. Hardwood has a high calorific value during combustion, while cork helps to shape particles and increase combustion stability. By mixing in this ratio, the advantages of both can be integrated, allowing the particles to have both high calorific value and maintain a good shape during combustion.
Wood chips mixed with other biomass: Wood chips account for 70% -90%, while other biomass (such as rice husks, peanut shells, corn stalks, etc.) account for 10% -30%. Adding other biomass can reduce costs while utilizing the characteristics of different raw materials to improve particle performance. For example, rice husk has a higher ash content, but it can increase the porosity of particles and improve the air permeability during combustion; Corn stover is rich in cellulose, which can improve the formability of particles to a certain extent.
Special purpose sawdust pellets
Barbecue wood chips: mainly made of apple wood, cherry wood and other fruit wood chips, with the addition of 10% -20% maple or walnut wood chips to enhance flavor. Fruit wood chips themselves have a unique fruity aroma, which can add wonderful flavors to food when burned, while maple or walnut wood chips can provide a stronger smoky flavor, making the flavor of grilled food more rich.
Wood chips with added binder: In some cases, a small amount of binder is added to improve the molding rate and strength of the particles. Generally, sawdust accounts for 95% -98%, and binders (such as starch, lignin, etc.) account for 2% -5%. Starch binder can play a good bonding role in the particle forming process, improving the hardness and stability of the particles; Lignin is a natural binder with good compatibility with wood chips, which can enhance the quality of particles without affecting combustion performance.
The above formula ratios are for reference only. In actual production, adjustments and optimizations need to be made based on specific raw material characteristics, production equipment, and market demand.
Production process
The production process of wood chips mainly includes raw material preparation, crushing, drying, granulation, cooling and screening. The following is a specific introduction:
1. Raw material preparation: Collect various types of sawdust raw materials, such as pine wood, birch wood, and other waste materials generated during wood processing, to ensure that the raw materials are free of impurities and excessive moisture. Different types of sawdust can be mixed according to product requirements to achieve ideal combustion performance and cost control.
2. Grinding: Use a grinder to grind the sawdust raw material into a suitable particle size, generally requiring a particle size of around 2-5 millimeters. The crushed wood chips have uniform particle size, which is beneficial for subsequent drying and granulation processes, improving the quality and forming rate of the particles.
3. Drying: Crushed wood chips usually contain a high amount of moisture and require drying treatment. The drying method can be natural air drying or using a dryer. Generally, the moisture content of wood chips is reduced to around 10% -15% to ensure smooth molding during the granulation process, while reducing smoke and odors generated during combustion.
4. Granulation: Send the dried wood chips into the granulator for granulation. The granulator compresses wood chips into granules through the squeezing action of the pressure roller and mold. During the granulation process, a small amount of binder such as starch, lignin, etc. can be added as needed to improve the strength and forming rate of the particles. Common granulators include ring mold granulators and flat mold granulators. Ring mold granulators have high production efficiency and are suitable for large-scale production; The flat mold granulator has a simple structure and is suitable for small-scale production or experimentation.
5. Cooling screening: The pelletized wood chips have a high temperature and need to be cooled by a cooler to reduce their temperature to room temperature. The cooled particles are screened through a vibrating screen to remove particles and powders that do not meet the particle size requirements, and then returned for re granulation to ensure the uniformity of the product’s particle size.
6. Packaging and storage: Qualified wood chips that have been screened are packaged, usually in plastic bags or woven bags, for easy storage and transportation. Packaged wood chips should be stored in a dry and ventilated warehouse to prevent moisture, mold, and spoilage.
In addition, throughout the entire production process, attention should be paid to controlling the process parameters of each link, and regular maintenance and upkeep of equipment should be carried out to ensure the production of stable and standard wood pellet products.
Production equipment
The production equipment for wood chips mainly includes crushing equipment, drying equipment, granulation equipment, cooling equipment, screening equipment, and packaging equipment. The following is a specific introduction:
1. Crushing equipment
Hammer crusher: Using a high-speed rotating hammer head to impact and shear materials, the sawdust raw material is crushed into smaller particles. It has the advantages of high crushing ratio, high production capacity, and simple structure, and is suitable for various hardness wood chips.
Disc crusher: It uses two relatively rotating disks, one of which is equipped with several grinding blocks, and the other disk is equipped with corresponding grinding grooves. The material is crushed and ground between the grinding blocks and grooves. This type of crusher has the advantages of good crushing effect, uniform particle size, and low energy consumption.
2. Drying equipment
Drum dryer: It consists of a tilted rotating drum and a heating device. Wood chips roll continuously inside the drum as it rotates, while fully exchanging heat with hot air to achieve drying. It has the advantages of high drying efficiency, large processing capacity, and simple operation, and is suitable for large-scale production.
Airflow dryer: Using high-speed hot air flow to blow up wood chips, making them suspended in the airflow, fully contacting and exchanging heat with the hot air flow, thus quickly drying. Its advantages are fast drying speed, good drying effect, small footprint, but relatively high energy consumption.
3. Granulation equipment
Ring mold granulator: mainly composed of ring mold, pressure roller, feeding mechanism, etc. During operation, materials are compressed by the pressure roller and form particles through the mold holes on the ring mold, which has the advantages of high production efficiency, good particle quality, and strong stability. It is currently one of the most widely used granulation equipment in the production of wood chips.
Flat mold granulator: The mold of the flat mold granulator is a horizontally placed disc, and the pressure roller rolls on the mold, squeezing the material through the small holes on the mold to form particles. It has a simple structure, easy operation, and relatively low price, making it suitable for small wood pellet production enterprises or family workshops to use.
4. Cooling equipment
Counter current cooler: using the principle of counter current cooling, particles enter from the top of the cooler, and cold air enters from the bottom. The two flow in opposite directions inside the cooler to evenly cool the particles. It has the advantages of good cooling effect, fast cooling speed, and small footprint.
Vibration type cooler: The cooler is vibrated by a vibration motor, and the particles are evenly distributed inside the cooler under the vibration. At the same time, cold air is blown into the cooler from the bottom to cool the particles. Its advantages are uniform cooling, less likely to clog, and simple maintenance.
5. Screening equipment
Vibration screen: Using the vibration generated by the vibration motor, particles are made to move in a circular or linear motion on the screen, thereby achieving the separation of particles of different sizes. It has the advantages of high screening efficiency, high precision, and simple structure, and is a commonly used screening equipment in the production of wood chips.
Rotary sieve: composed of a rotating cylindrical screen mesh and a driving device. Particles enter from one end of the cylinder, and under the rotation of the cylinder, particles smaller than the mesh size fall through the screen mesh, while particles larger than the mesh size are discharged from the other end of the cylinder. Suitable for situations with large processing capacity and low requirements for screening accuracy.
6. Packaging equipment
Automatic quantitative packaging machine: capable of automatically completing packaging processes such as material measurement, filling, and sealing, with advantages such as high packaging accuracy, fast speed, and easy operation. Can be adjusted according to different packaging specifications and requirements, suitable for large-scale production.
Manual packaging machine: With a simple structure and affordable price, it is suitable for small production enterprises or situations with low output. Manual material measurement and packaging operations are required, resulting in relatively low packaging efficiency but high flexibility.
Application
Wood chips have various applications, mainly including the following aspects:
Energy sector
Heating fuel: Wood chips have high combustion efficiency, generate a large amount of heat, and produce less pollutants during the combustion process, making them a high-quality heating fuel. It can be used for heating in homes, schools, factories, and other places, and is burned through specialized pellet heating furnaces or biomass boilers to provide warmth indoors.
Power generation fuel: In some biomass power plants, wood pellets are used as fuel to generate steam through combustion, which drives a steam turbine to generate electricity. Compared with traditional fossil fuels, using wood pellets for power generation can reduce greenhouse gas emissions such as carbon dioxide and has good environmental benefits.
Industrial sector
Industrial boiler fuel: Many industrial production processes require boilers to provide steam or heat, and wood chips can be used as fuel for boilers, replacing traditional fuels such as coal and heavy oil. This can not only reduce the fuel costs of enterprises, but also reduce environmental pollution and meet environmental protection requirements.
Raw materials for activated carbon production: Wood chips can be processed into activated carbon through high-temperature carbonization and activation processes. Activated carbon has strong adsorption properties and is widely used in industries such as water treatment, air purification, food processing, and pharmaceuticals to adsorb impurities, pigments, odors, etc.
Agriculture
Soil amendment: Applying wood chips into the soil can improve its structure, increase its permeability and water retention, and promote the growth and development of plant roots. Meanwhile, wood chips gradually decompose in the soil, providing organic matter and increasing soil fertility.
Edible mushroom cultivation substrate: Wood chips are a good substrate for cultivating edible mushrooms, such as shiitake mushrooms, fungus, and shiitake mushrooms. It provides necessary nutrition and support for the growth of edible fungi, helping to improve their yield and quality.
Other areas
Barbecue fuel: As mentioned earlier, wood chips made from apple wood, cherry wood, and other fruit trees are high-quality barbecue fuels. During the barbecue process, the smoke and aroma generated by the burning of wood chips can give the food a unique flavor, making the grilled food more delicious.
Pet bedding: Processed wood pellets have good water absorption and deodorization properties, and can be used as pet bedding, such as for cat litter, small pets, etc. They can effectively absorb pet excrement and odors, and maintain a clean and hygienic feeding environment.