PEEK masterbatch is a type of injection molding masterbatch made from polyetheretherketone (PEEK) material. It is a semi crystalline, thermoplastic special engineering plastic with excellent properties such as high temperature resistance, self-lubricating, and corrosion resistance. PEEK masterbatch is designed specifically for injection molding processes, and various shapes and sizes of products can be manufactured through injection molding processes.
Types
PEEK masterbatch can have multiple types according to different classification standards. The following are some common classification methods and corresponding types:
According to the classification of additives
Enhanced PEEK masterbatch: Glass fiber, carbon fiber and other reinforcing materials are added to PEEK resin to improve its mechanical strength, rigidity and heat resistance. For example, adding carbon fiber to PEEK masterbatch can significantly improve the strength and modulus of the product, while maintaining good wear resistance and chemical corrosion resistance. It is commonly used in fields such as aerospace and automotive manufacturing that require high material performance.
Filled PEEK masterbatch: Adding fillers such as calcium carbonate, talcum powder, mica, etc. can reduce costs and improve certain properties of the material, such as increasing dimensional stability and reducing shrinkage rate. Filled PEEK masterbatch is widely used in fields such as electronics, electrical appliances, and mechanical manufacturing.
Flame retardant PEEK masterbatch: By adding flame retardants, PEEK masterbatch has good flame retardant properties, which can meet the requirements of different application scenarios for material fire safety. Commonly used in industries such as rail transit, wires and cables that have strict requirements for flame retardancy.
Classification based on processing performance
High flowability PEEK masterbatch: Through special formula design and processing technology, it has low melt viscosity and good flowability, making it easy to form complex shaped products in injection molding, extrusion and other processing processes, improving production efficiency and product quality. Suitable for manufacturing precision instrument parts, medical device components, etc.
Heat resistant PEEK masterbatch: It has higher thermal stability and heat-resistant deformation temperature, and can be used for a long time in high temperature environments without significant performance degradation. Commonly used in the manufacturing of components in high-temperature working environments such as aircraft engines and industrial furnaces.
Classified by application field
PEEK masterbatch for aerospace: The performance requirements for the material are extremely strict, requiring high strength, high heat resistance, lightweight and other characteristics to meet the stringent requirements for component reliability and performance in the aerospace field.
PEEK masterbatch for automotive industry: It is required to have good mechanical properties, wear resistance, oil resistance, weather resistance, etc. It can be used to manufacture automotive engine components, transmission system components, automotive electronic equipment casings, etc., which helps to achieve lightweighting and high performance of automobiles.
PEEK masterbatch for electronic appliances: It needs to have excellent electrical insulation performance, arc resistance, dimensional stability, and processing performance, and is commonly used in the manufacturing of electronic component packaging materials, integrated circuit sockets, wire and cable insulation layers, etc.
PEEK masterbatch used in the medical field: It is required to have good biocompatibility, non toxicity, corrosion resistance, and X-ray transparency, and can be used to manufacture artificial joints, dental implants, medical device casings, etc.
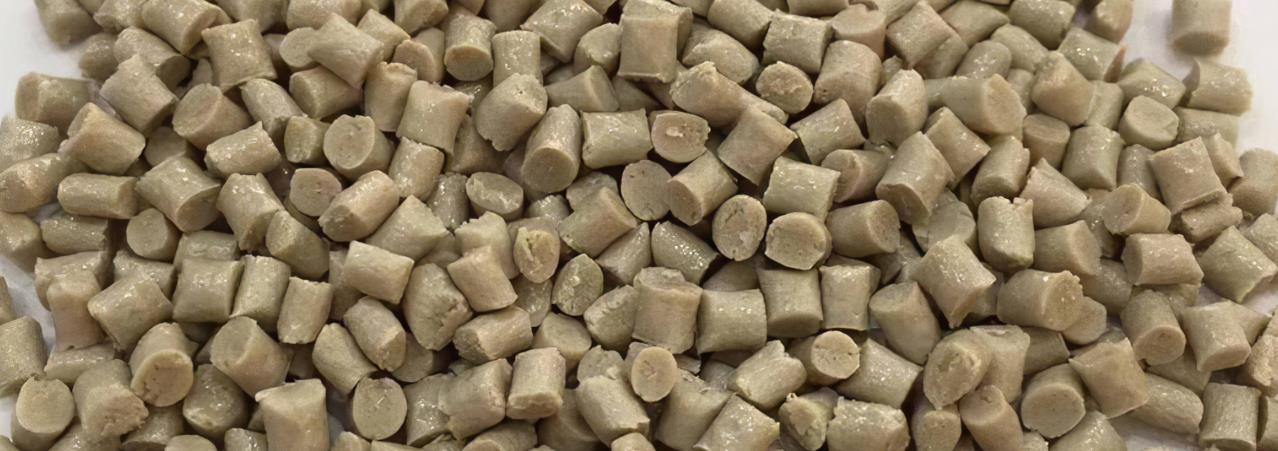
Formula ratio
The formula ratio of PEEK masterbatch may vary depending on the type of masterbatch and application requirements. The following are typical formula ratio ranges for several common PEEK masterbatch:
Enhanced PEEK masterbatch
PEEK resin: 60% -80%
Reinforcement material (glass fiber/carbon fiber): 20% -40%
Glass fiber or carbon fiber can significantly enhance the mechanical properties of PEEK, such as tensile strength, flexural strength, and modulus. Carbon fiber reinforcement has a better effect and can also endow the material with conductivity, but the cost is also higher.
Filled PEEK masterbatch
PEEK resin: 70% -90%
Fillers (calcium carbonate/talc/mica, etc.): 10% -30%
Fillers can reduce costs, improve dimensional stability and rigidity, but they may sacrifice the toughness and strength of the material to some extent. Calcium carbonate has low cost, talc powder can improve the surface quality of materials, and mica can enhance the heat resistance and electrical insulation of materials.
Flame retardant PEEK masterbatch
PEEK resin: 75% -90%
Flame retardant: 10% -25%
The type and amount of flame retardant should be determined according to specific flame retardant requirements. Common flame retardants include halogen flame retardants, phosphorus flame retardants, nitrogen flame retardants, etc. Halogen flame retardants have good flame retardant effects, but may pose certain hazards to the environment and human health; Phosphorus based and nitrogen based flame retardants are relatively environmentally friendly and can also have a certain plasticizing effect, improving the processing performance of materials.
High fluidity PEEK masterbatch
PEEK resin: 90% -95%
Flow modifier: 5% -10%
Flow modifiers are generally low molecular weight polymers or surfactants that can reduce the melt viscosity of PEEK, improve its flowability, and enhance processing performance. However, excessive addition may affect the mechanical properties of the material.
Heat resistant PEEK masterbatch
PEEK resin: 85% -95%
Heat resistant additive: 5% -15%
Heat resistant additives can be high-temperature resistant inorganic fillers or organic compounds, such as alumina, boron nitride, polybenzimidazole, etc., which can improve the thermal stability and heat deformation temperature of PEEK, but may increase the material cost.
The above formula ratios are for reference only. In actual production, optimization and adjustment should be made based on specific application requirements, processing technology, and cost factors.
Production process
The production process of PEEK masterbatch usually includes steps such as raw material preparation, mixing, extrusion, granulation, packaging, etc. The following is a specific introduction:
1. Raw material preparation
Resin selection: Select the appropriate type of PEEK resin particles based on product performance requirements, and ensure that their purity, molecular weight distribution, and other indicators meet production standards.
Additive preparation: Accurately weigh various additives according to the formula requirements, such as reinforcing materials, fillers, flame retardants, flow modifiers, heat-resistant additives, etc. Ensure that the particle size and purity of the additives meet the process requirements.
2. Mixing
Pre mixing: Add PEEK resin and additives to a high-speed mixer or kneading machine for pre mixing, so that each component is initially dispersed evenly. By the high-speed rotation of the stirring blade, shear and friction forces are generated to promote the mixing of materials.
Mixing: The pre mixed material enters the mixing machine for further mixing. There are two relatively rotating rotors inside the mixer, which mix and disperse PEEK resin and additives thoroughly under high temperature, high pressure, and strong shear, forming a uniform mixture. The mixing temperature is generally controlled at 300-350 ℃ for 10-30 minutes.
3. Extrusion
Heating up: Add the mixed material into the hopper of the extruder, and the barrel of the extruder is heated up by electric heating or thermal oil heating. Generally, from the hopper end to the machine head direction, the temperature of the barrel gradually increases, causing the material to gradually melt during the extrusion process.
Screw extrusion: Under the rotation of the screw, the material moves forward in the barrel, while being subjected to the shear and compression of the screw, further plasticizing and mixing. The parameters of screw speed, aspect ratio, compression ratio, etc. are optimized and adjusted according to material characteristics and product requirements. The extrusion temperature is usually between 350-400 ℃ to ensure that the PEEK resin is fully melted and the additives are evenly dispersed in the melt.
4. Granulation
Underwater granulation: The extruded molten material is extruded into strips or filaments through a die and directly enters the cooling water tank of the underwater granulator. In water, the material rapidly cools and solidifies, and then it is cut into uniform particles by a rotating pellet cutter. The advantages of underwater granulation are regular particle shape, smooth surface, good cooling effect, which can effectively avoid particle adhesion and oxidation.
Air cooled granulation: Another method is air cooled granulation, in which the extruded material passes through the die and is naturally cooled in the air or accelerated by a forced air cooling device before being cut into pellets. The equipment for air-cooled granulation is relatively simple, but the cooling speed of the particles is slow, which may affect production efficiency and particle quality.
5. Packaging
Screening: The PEEK masterbatch after granulation is screened through a vibrating screen or rotary vibrating screen to remove particles that are too large or too small, ensuring the uniformity of the product’s particle size.
Packaging: Qualified products that have been screened are packaged in specialized bags or containers, usually sealed to prevent moisture absorption, oxidation, or other contamination of the masterbatch. The packaged products are stored in a dry and ventilated warehouse, waiting for transportation and sale.
Throughout the entire production process, it is necessary to strictly control the process parameters of each link, such as temperature, pressure, speed, time, etc., and monitor and test the product quality through online detection and offline analysis to ensure that the produced PEEK masterbatch meets relevant standards and customer requirements.
Production equipment
The equipment for producing PEEK masterbatch mainly includes the following types:
Mixing equipment
High speed mixer: used to preliminarily mix PEEK resin with additives, and achieve a certain degree of uniform dispersion of the material in a short period of time through high-speed rotating stirring blades. It has the characteristics of high mixing efficiency and good mixing effect.
Internal mixer: capable of fully mixing and dispersing PEEK resin with various additives under high temperature, high pressure, and strong shear, ensuring uniform material mixing and laying a good foundation for subsequent processing.
Extrusion equipment
Single screw extruder: With a simple structure and easy operation, it is suitable for situations with low production requirements or low material processing difficulty. It pushes the material forward inside the barrel through the rotation of the screw, while using the heating device of the barrel to gradually melt the material, achieving plasticization and extrusion.
Twin screw extruder: With excellent mixing, dispersing, and conveying capabilities, it can better handle high viscosity and difficult to process materials, such as the addition of large amounts of reinforcing materials or fillers in PEEK masterbatch production. The meshing structure of twin-screw ensures that the material is subjected to stronger shearing and kneading during the extrusion process, which helps to improve product quality and production efficiency.
Granulation equipment
Underwater granulator: composed of mold head, cooling water tank, cutting device, etc. The extruded molten material is formed into strips or filaments through the die head, and directly enters the cooling water tank for rapid cooling and solidification. Then, it is cut into uniform particles by a cutting knife. The particles produced by this device have regular shapes, smooth surfaces, high quality, and a relatively clean and efficient production process.
Air cooled granulation equipment: including air cooling system and granulation device. After the extruded material passes through the die, it is naturally cooled in the air or accelerated by a forced air cooling device to reach a certain hardness before being cut into pellets. The equipment structure is relatively simple and the cost is low, but the cooling speed is slow, and the production efficiency may not be as good as that of underwater granulators.
Auxiliary equipment
Feeding machine: used to automatically transport raw materials to the hopper of mixing equipment or extruder, achieve automatic feeding of raw materials, improve production automation level, and reduce manual labor intensity. Common ones include screw feeders, vacuum feeders, etc.
Drying equipment: Before production, PEEK resin and additives are dried to remove moisture and volatile substances, preventing defects such as bubbles and silver wires during processing, which can affect product quality. Common drying equipment includes ovens, dehumidifiers, and dryers.
Screening equipment: such as vibrating screens, rotary vibrating screens, etc., used to screen PEEK masterbatch after granulation, remove oversized or undersized particles, ensure the uniformity of product particle size, and improve product quality.
Packaging equipment: including automatic packaging machines, sealing machines, etc., used to package qualified products after screening, achieve quantitative packaging and sealed packaging, prevent moisture absorption, oxidation or other contamination of masterbatch, and ensure stable product quality during storage and transportation.
PEEK masterbatch extruder
Kerke’s masterbatch extruder can be used to produce PEEK masterbatch. Our PEEK masterbatch extruder has multiple models to choose from, which can meet different production requirements.
-
Laboratory Twin Screw Extruder
When will you need a lab twin screw extruder? If you want to make trials and tests of…
-
Parallel Twin Screw Extruder
Our Parallel Co-rotating twin screw extruder is designed for compounding and masterbatch making with an output capacity from…
-
Triple (3 screws) Extruder
3 Screws extruder is a new technology that has many advantages. The triple screw extruder is mainly used…
-
Double-Stage Extrusion System
Mother-baby extrusion system is designed for special materials which can not process on one stage extruder, the first…
-
Banbury Kneader Compounding Line
Our kneader + extruder is designed for making special applications with an output capacity from 30kg/h to 1000kg/h.…
-
Cutting System / Pelletizing System
Different material needs different cutting system, Kerke provides all kinds of cutting system, here is the explanation of…
Related requirements
The extruder plays a key role in the production of PEEK masterbatch, and the following are some requirements for the extruder:
High temperature performance
Temperature resistance: As the processing temperature of PEEK resin is usually between 350-400 ℃, the barrel, screw and other components of the extruder need to be made of high-temperature resistant alloy materials, such as nickel based alloys, to ensure good strength, hardness and corrosion resistance at high temperatures, and to prevent component deformation, wear or chemical reactions.
Temperature control accuracy: Accurate temperature control is crucial during the extrusion process. The extruder needs to be equipped with a high-precision temperature control system, such as thermocouples, temperature control instruments, and heating and cooling devices, which can control the temperature of each heating section within ± 2 ℃ of the set value, ensuring uniform melting of PEEK resin and avoiding unstable material properties or local overheating and undercooling caused by temperature fluctuations.
Screw design
Length to diameter ratio: A suitable length to diameter ratio is crucial for the production of PEEK masterbatch. Generally speaking, a length to diameter ratio between 25-40 is more suitable. Longer screws can provide longer material conveying and plasticizing distances, allowing PEEK resin to be fully mixed, melted, and homogenized with additives, thereby improving product quality.
Screw structure: The structure of the screw should be optimized and designed according to the formula and production process of PEEK masterbatch. Usually, gradient or mutation type screws are used. Gradient type screws are suitable for processing materials with high viscosity and poor flowability, which can gradually heat up and melt the materials in the screw, reducing shear heat and pressure fluctuations; The mutant screw is suitable for the production of PEEK masterbatch with a large amount of fillers or reinforcing materials added, which can generate strong shear force and facilitate the dispersion and mixing of materials. In addition, appropriate mixing and metering sections should be installed on the screw to further improve the uniformity of material mixing and the stability of extrusion volume.
Pressure control
Pressure stability: During the extrusion process, stable pressure is one of the key factors in ensuring product quality and production efficiency. The hydraulic system or mechanical transmission system of the extruder should be able to provide stable extrusion pressure, with a fluctuation range controlled within ± 5%, to avoid unstable extrusion volume, product size deviation, or surface defects caused by pressure fluctuations.
Pressure regulation range: The extruder should have a wide pressure regulation range to meet the requirements of different formulations and production processes. For example, in the production of PEEK masterbatch with different types and contents of additives added, the extrusion pressure can be flexibly adjusted according to the characteristics of the material and extrusion requirements to ensure smooth extrusion of the material and achieve the expected product performance.
Production and efficiency
Production capacity: Select extruders with appropriate production capacity based on production scale and market demand. Generally speaking, the output of single screw extruders is relatively low and suitable for small-scale production or experimental research; The output of twin-screw extruders is relatively high, which can meet the needs of large-scale industrial production. When selecting an extruder, parameters such as screw diameter, speed, and motor power should be comprehensively considered based on actual production needs to ensure that the extruder can achieve the expected output target.
Production efficiency: To improve production efficiency, extruders should have the characteristics of fast start-up, stable operation, and efficient extrusion. At the same time, an automated control system should be equipped to achieve real-time monitoring and adjustment of the extrusion process, reduce manual intervention, and improve production efficiency and product quality consistency. In addition, the maintenance of the extruder should be convenient and fast to reduce equipment downtime and improve equipment utilization.
Corrosion Resistance
Contact with material components: Due to the use of corrosive additives such as certain flame retardants and lubricants in the production process of PEEK masterbatch, parts in contact with the material in the extruder, such as the inner wall of the barrel, the surface of the screw, and the die head, need to be treated with anti-corrosion measures, such as chrome plating, nickel plating, or spraying corrosion-resistant coatings, to improve the corrosion resistance of the parts, extend the service life of the equipment, and ensure that product quality is not affected by corrosive substances.
Application
PEEK masterbatch has excellent properties and is therefore widely used in various fields such as aerospace, automotive manufacturing, electronics and electrical, medical, etc. The following is a specific introduction:
Aerospace field
Component manufacturing: PEEK masterbatch can be used to manufacture structural components of aircraft, engine components, etc. Its high strength, high stiffness, and good fatigue resistance can withstand various complex stresses of the aircraft during flight; Meanwhile, its excellent high temperature resistance enables it to maintain stable performance even in high-temperature engine environments, which helps reduce aircraft weight, improve fuel efficiency, and enhance overall aircraft performance.
Aviation interior: In terms of aviation interior, PEEK masterbatch can be used to manufacture seat frames, luggage racks, etc. It not only has good mechanical performance, but also meets the strict requirements of flame retardant, low smoke, non-toxic and other materials for aviation interiors, improving the safety and comfort of aircraft interiors.
Automotive manufacturing field
Engine system: In automotive engines, PEEK masterbatch can be used to manufacture components such as piston rings, valve seals, spark plug insulators, etc. It has high temperature resistance, wear resistance, and chemical stability, and can work stably for a long time in the high temperature, high pressure, and harsh chemical environment of the engine, improving the reliability and durability of the engine, while helping to reduce the weight of the engine and improve the fuel economy of the car.
Electronic and electrical systems: In automotive electronic and electrical systems, PEEK masterbatch can be used to manufacture connectors, sockets, coil frames, etc. Its excellent insulation performance and chemical corrosion resistance can ensure the stable operation of electronic and electrical components in complex automotive electrical environments, prevent electrical faults and short circuits, and improve the reliability and safety of automotive electronic systems.
Electronic and electrical field
Semiconductor manufacturing: In semiconductor manufacturing equipment, PEEK masterbatch can be used to manufacture wafer carriers, chip fixtures, electron beam exposure machine components, etc. It has excellent chemical corrosion resistance, low friction coefficient, and high-precision dimensional stability, which can meet the strict requirements for materials in the semiconductor manufacturing process, ensuring the production accuracy and quality of semiconductor devices.
Wire and cable: PEEK masterbatch can be used to manufacture insulation layers and sheaths for high-performance wire and cable. It has good insulation performance, high temperature resistance, and mechanical properties, which can ensure the safe and reliable operation of wires and cables in high temperature and high voltage environments. It is widely used in fields such as aerospace, nuclear energy, and petrochemicals that require high performance of wires and cables.
Medical field
Medical devices: PEEK masterbatch can be used to manufacture medical devices such as artificial joints, spinal fusion devices, dental implants, etc. Its good biocompatibility, similar to the elastic modulus of human bones, can reduce the stress shielding effect between implants and human tissues, and lower the risk of implant loosening and fracture; At the same time, its good corrosion resistance and wear resistance enable it to work stably in the human body for a long time, improving the service life and therapeutic effect of medical devices.
Medical equipment components: In medical equipment, PEEK masterbatch can be used to manufacture parts such as handles for surgical instruments, casings for endoscopes, gears and bearings for medical devices. Its high strength, high toughness, and good processing performance can meet the precision, strength, and reliability requirements of medical equipment components, while being easy to disinfect and clean, in line with the hygiene standards of the medical industry.